Hydrogen sulphide detected in a bilge tank
- Safety Flash
- Published on 25 November 2021
- Generated on 29 April 2025
- IMCA SF 32/21
- 3 minute read
Jump to:
During routine transfer of bilge water from engine room bilge wells to the bilge water tank, the crew noticed the smell of “rotten eggs” from the bilge tank vent. Immediately the transfer was stopped.
During measuring the vent pipe with the Dräger multi-gas meter it was confirmed 453 ppm of Hydrogen Sulphide (H2S) was detected.
Preventive actions were taken to ensure the gasses did not enter the accommodation. The quick response of the vessel crew prevented a serious accident.
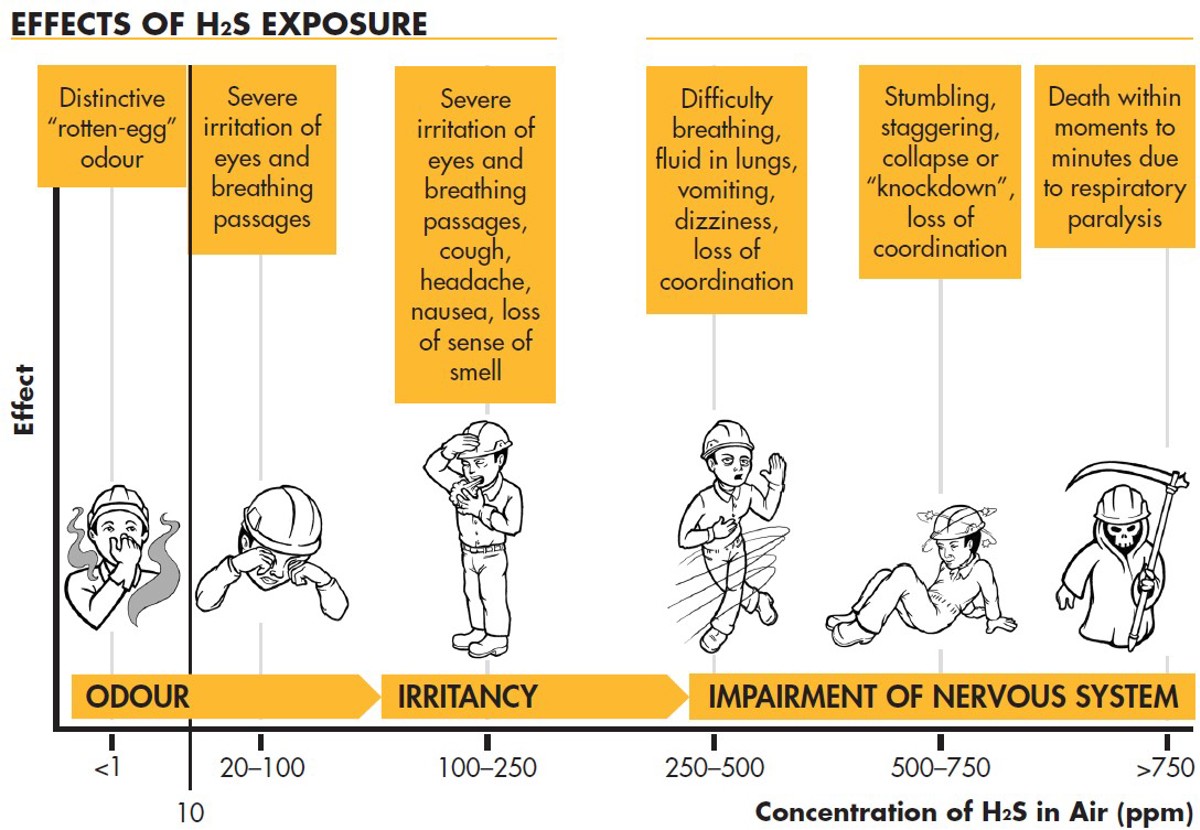
The immediate hazard was of a dangerous or even lethal atmosphere (high H2S concentration).
Seawater in (bilge) tanks, especially in the engine room, mixed with various residues and biodegradable detergents are a perfect place for the development of dangerous levels of H2S.
Failure to recognise the dangers could have resulted in explosion, intoxication or even loss of life.
What went wrong?
Technical
- Bilge tank had not been dealt with or emptied for a longer period – it had not filled up.
- Regular inspection of the tank was not easily possible.
- Several corners of the tank had built up (stone) residue, which was not easily removed.
Organisational
- Lack of knowledge: during the communication with external parties it was found that some parties were uncertain how to handle the removal of the sludge from the tank without contaminating the atmosphere of the surrounding ER spaces.
- The on-location specialist was occupied and not able to assist immediately.
- There was not a suitable berth available for tank cleaning.
- The required vacuum and ventilation equipment were not available and there was a delay of some days before the final removal of sludge and tank cleaning.
Actions taken
- Stopped the transfer (“Stop the Job”).
- Measured the H2S concentration.
- Informed emergency response team and client.
- Connected flexible hose to vent pipe to route gases away from the accommodation.
- Requested assistance from local agencies on removal of the bilge residue and tank cleaning.
- Constant monitoring by measuring device with crew in full respiratory protection.
- Removal of bilge water and cleaning of the tank by a specialised company.
- Gas-free certificate issued.
Lessons learned
Review of vessel machinery cleaning practice:
- Clean machinery spaces with detergents when the ship is in port, preferably using fresh water.
- Check if use of bio-degradable detergents are necessary or possibility for replacement additives and cleaning agents.
Members may also wish to review H2S, the killer [a booklet from the government of Alberta; similar information from other governments is available.]
Related Safety Flashes
-
IMCA SF 01/12
25 January 2012
IMCA Safety Flashes summarise key safety matters and incidents, allowing lessons to be more easily learnt for the benefit of the entire offshore industry.
The effectiveness of the IMCA Safety Flash system depends on the industry sharing information and so avoiding repeat incidents. Incidents are classified according to IOGP's Life Saving Rules.
All information is anonymised or sanitised, as appropriate, and warnings for graphic content included where possible.
IMCA makes every effort to ensure both the accuracy and reliability of the information shared, but is not be liable for any guidance and/or recommendation and/or statement herein contained.
The information contained in this document does not fulfil or replace any individual's or Member's legal, regulatory or other duties or obligations in respect of their operations. Individuals and Members remain solely responsible for the safe, lawful and proper conduct of their operations.
Share your safety incidents with IMCA online. Sign-up to receive Safety Flashes straight to your email.