Failure of steel wire sling
- Safety Flash
- Published on 21 December 2017
- Generated on 12 July 2025
- IMCA SF 32/17
- 3 minute read
Jump to:
During offshore wind farm construction, pull wires were being laid.
What happened?
One small vessel was acting as a winch vessel, and another as an anchor. These vessels were connected with a steel wire rope sling. During wire pull operations, the steel wire rope sling failed.
When the wire failed the energy stored in the steel wire rope sling and the rigging arrangement was released, causing damage to the rigging arrangement, load cell, Panama chock and the deck of the winch vessel. There were no injuries, as a ‘clear deck’ instruction was in place.
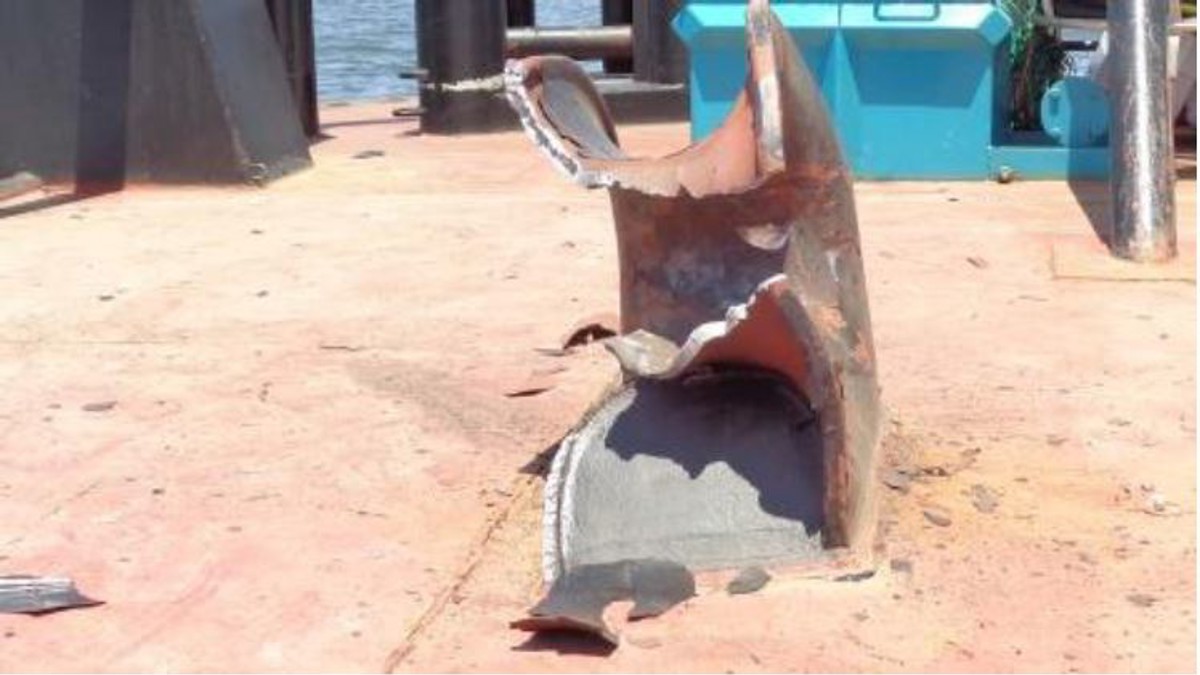
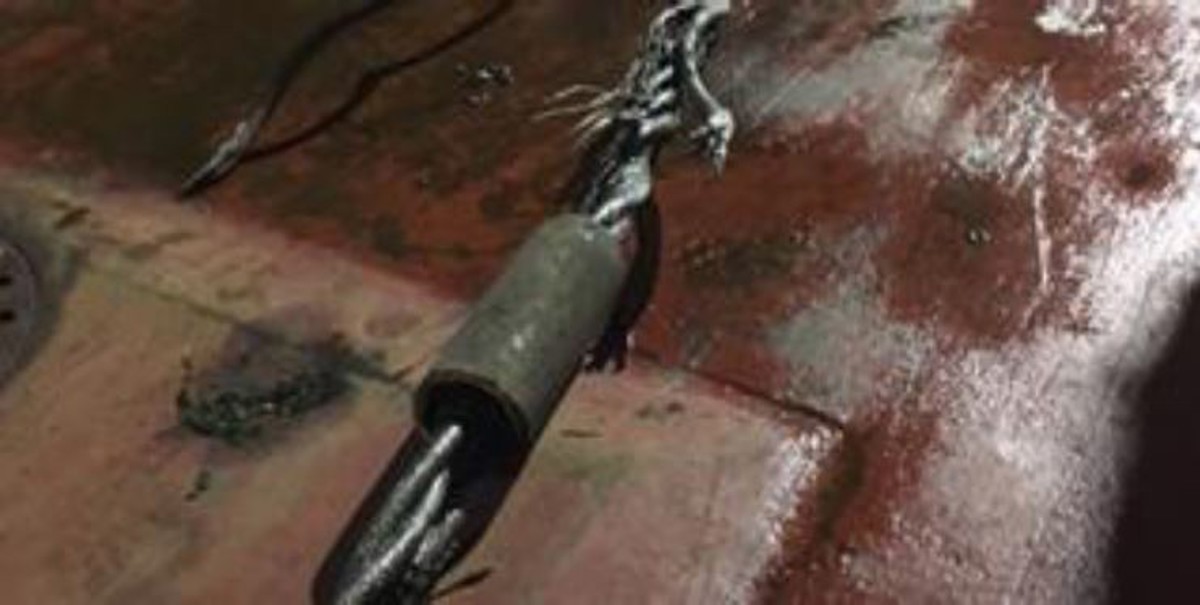
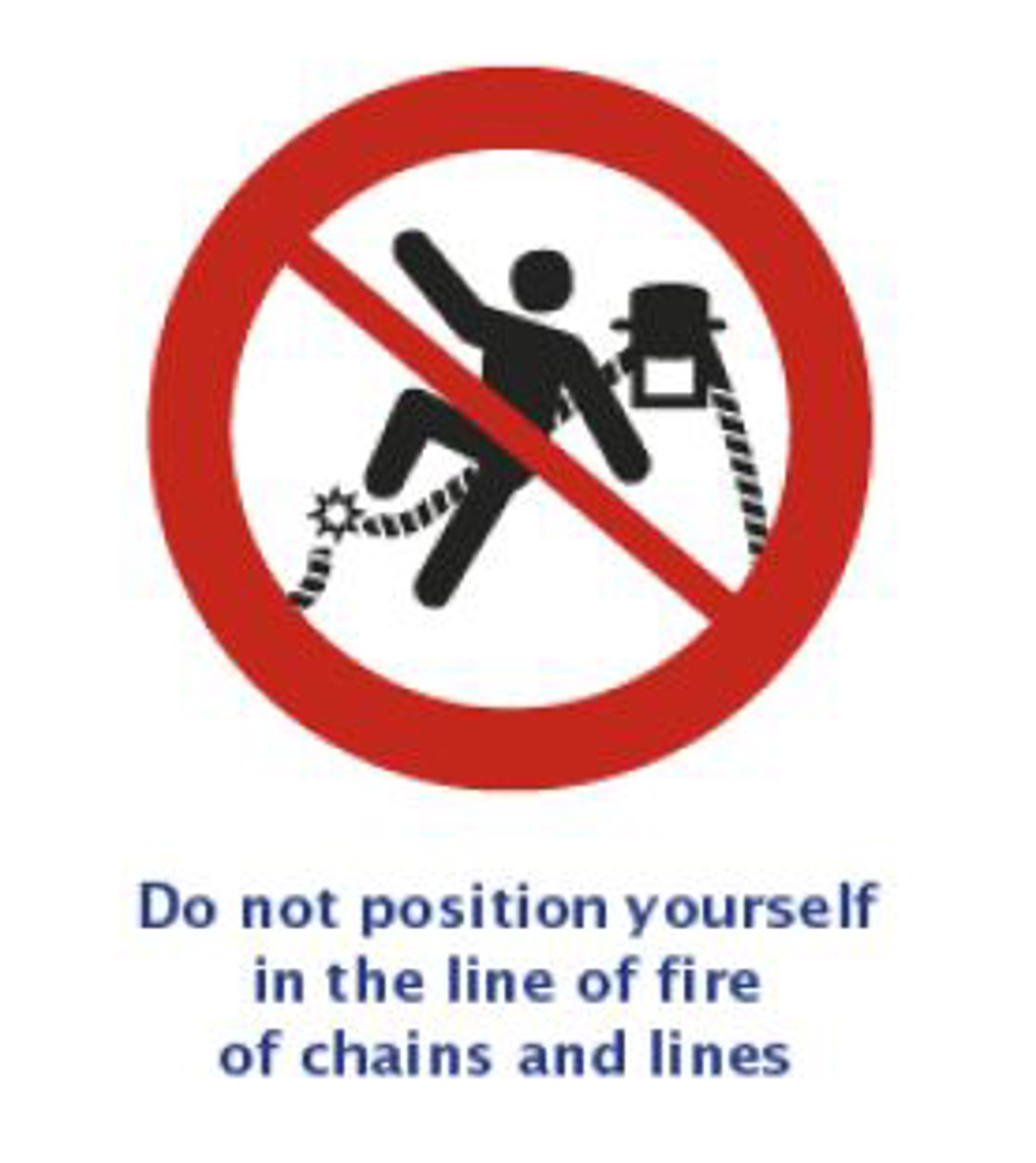
What went wrong? What were the causes?
The wire failed at the splice inside the ferrule following an increase in tension. It was concluded that the mechanism of failure was a low-cycle fatigue fracture.
Further detailed investigation showed that dynamic forces on the hold-back or anchor arrangements were higher than anticipated, leading to the overstressing and therefore the failure of the wire. These peak forces were not picked up during manual logging.
Similar failures have occurred due to the splice failing under higher than anticipated dynamic loading causing the splice to pull from the ferrule.
Lessons learnt
- Because the ‘clear deck’ instruction was followed, ensuring that no personnel were in the ‘line of fire’, there were no injuries.
- One of the investigation findings was that an incorrect calculated sling breaking load (CSBL) was assumed. Hence the working load limit (WLL) of the steel wire sling was also incorrect. When a steel wire sling is assembled, a reduction in WLL for the assembly is applicable depending on the end termination and the factor of safety. In this case, the termination efficiency (KT) for a ‘super splice’ or ‘super loop’ is 90%. For example, if the steel wire had a CSBL of 100 Tonnes, a factor of safety of 3:1 and a termination efficiency of 0.9, then the assembled wire sling should have a WLL of 30 Tonnes – i.e. CSBL = WLL x SF x KT. This reduction was not included on the certificate’s WLL that came with the assembled wire rope sling. Clear marking, certification and utilisation of equipment must be checked thoroughly when new equipment is delivered.
- The forces on the wires were measured via a load cell. These readings of the load cell were logged manually. Data logging should be automated allowing continuous (digital) logging of the load cell data. This data can then be used to check which forces are being exerted on wires and if workability limits are reached.
Members may wish to refer to the following incidents:
- Near-miss: Corrosion caused crane boom failure during heavy lifting
- Failure of hose reel bearing housing
IMCA Safety Flashes summarise key safety matters and incidents, allowing lessons to be more easily learnt for the benefit of the entire offshore industry.
The effectiveness of the IMCA Safety Flash system depends on the industry sharing information and so avoiding repeat incidents. Incidents are classified according to IOGP's Life Saving Rules.
All information is anonymised or sanitised, as appropriate, and warnings for graphic content included where possible.
IMCA makes every effort to ensure both the accuracy and reliability of the information shared, but is not be liable for any guidance and/or recommendation and/or statement herein contained.
The information contained in this document does not fulfil or replace any individual's or Member's legal, regulatory or other duties or obligations in respect of their operations. Individuals and Members remain solely responsible for the safe, lawful and proper conduct of their operations.
Share your safety incidents with IMCA online. Sign-up to receive Safety Flashes straight to your email.