Serious finger injury during valve installation
- Safety Flash
- Published on 18 October 2016
- Generated on 18 April 2025
- IMCA SF 28/16
- 4 minute read
Jump to:
A Member has reported an incident in which a second engineer suffered a serious injury leading to the loss of the tip of his left middle finger.
What happened?
The incident occurred during valve operation function tests on a remotely operated pneumatic controlled valve for a vessel fuel system. There were some issues with the opening and closing of one particular valve. The decision was taken to change out the valve.
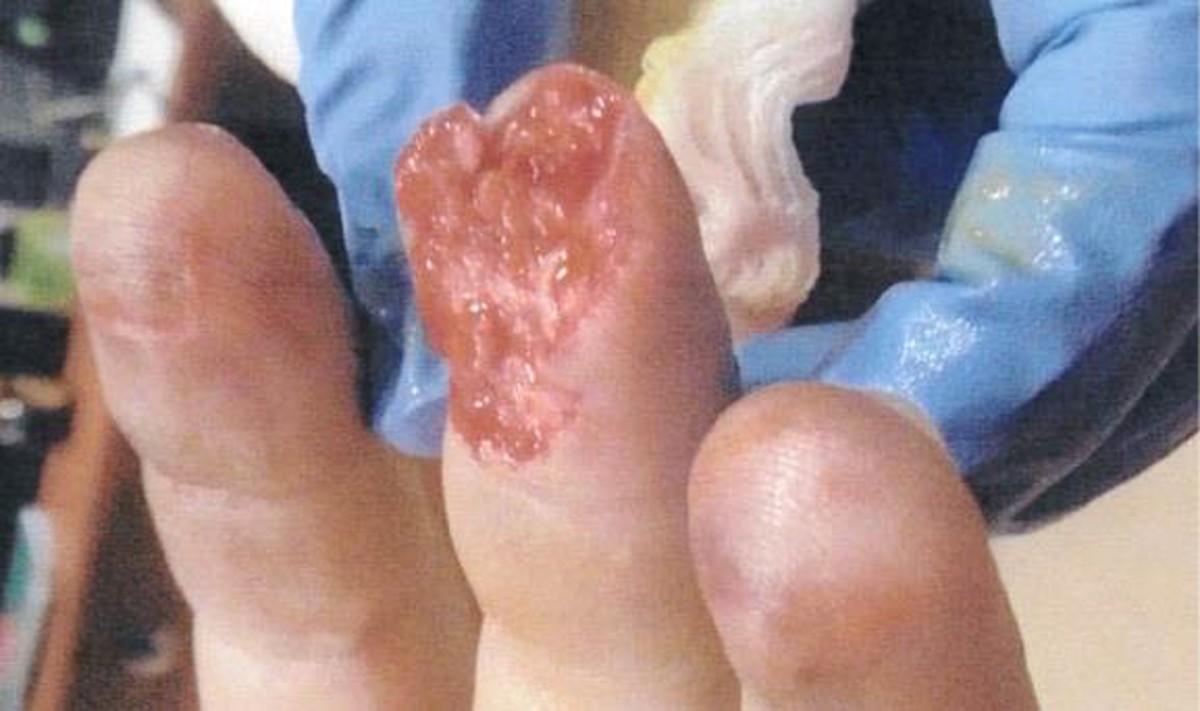
The second engineer used an air-gun to supply low pressure compressed air to the valve, instead of reconnecting the valve to the system air controlling pneumatic valves. During this pre mounting test, the valve did not open properly and got stuck in a half-open position. The engineer tried to move the valve-flap with his fingers. At the same time, he supplied air to the actuator with the air-gun. The valve-flap suddenly closed, and the tip of his left middle finger was cut off by the valve-flap. The engineer was medevacked.
Our member’s investigation revealed the following:
- The immediate cause of the incident was the engineer using his fingers directly on the valve-flap instead of using the correct tools.
- The job was considered routine by the engine crew.
- The valve was not secured whilst the engineer tested it.
- There was no rush when it came to replacing the valve; the crew could have used sufficient time to plan the operation in more detail and agree upon which equipment should be used.
- The engineer carried out simultaneous tasks – he was holding the air-gun with one hand, the valve with the left hand and simultaneously tried to move the valve-flap with his fingers, taking a shortcut.
Our member considered that some of the root causes of the incident were:
-
- inadequate or substandard planning
- the use of short-cuts
- Some of the causal factors were as follows
- Poor or inadequate risk assessment: the engineer should have been aware that the valve-flap could suddenly close, and have prepared for it
- Routine – complacency and low awareness of risk: since the replacement of valves was considered a routine job and carried out regularly, it is possible that the engineer and motorman were not as alert as they ought to have been during this specific operation, nor did they have sufficient awareness of risk, and they did not properly assess the danger when it came to moving parts
- PPE: gloves were not used by the engineer during the replacement of the valve. Company procedures require that gloves in the engine room should be ‘readily available and worn as required in work permit/risk assessment’
- Failure to follow procedures: company procedures for Permit to Work state that work on the fuel system should been covered by a work permit. In order to replace the valve, the fuel system/pipe should have been isolated in order to avoid any risk of fuel entering the affected area, and the air system controlling pneumatic valves should have been isolated/disconnected. These would have been covered by the work permit and resulted in use of the Lock Out Tag Out procedure/checklist. The engine crew assessed the job to be a low risk routine job and took the view that a Permit to Work was not required.
Following the ‘safety stand down’ and discussion, our member took the following actions:
- Further review of company’s Permit to Work procedures, Lock Out Tag Out System procedures, and Risk Assessment procedures.
- A renewed focus to be on finger/hand injuries.
- Further review of risk assessment for work on fuel system and changing of pneumatic valves.
IMCA publishes a range of safety promotional material which will be useful to members in addressing this incident. In particular, members’ attention is drawn to the pocket card ‘watch your hands‘.
Related Safety Flashes
-
IMCA SF 11/12
26 October 2012
-
IMCA SF 02/11
25 February 2011
IMCA Safety Flashes summarise key safety matters and incidents, allowing lessons to be more easily learnt for the benefit of the entire offshore industry.
The effectiveness of the IMCA Safety Flash system depends on the industry sharing information and so avoiding repeat incidents. Incidents are classified according to IOGP's Life Saving Rules.
All information is anonymised or sanitised, as appropriate, and warnings for graphic content included where possible.
IMCA makes every effort to ensure both the accuracy and reliability of the information shared, but is not be liable for any guidance and/or recommendation and/or statement herein contained.
The information contained in this document does not fulfil or replace any individual's or Member's legal, regulatory or other duties or obligations in respect of their operations. Individuals and Members remain solely responsible for the safe, lawful and proper conduct of their operations.
Share your safety incidents with IMCA online. Sign-up to receive Safety Flashes straight to your email.