Focus on third-party dropped objects
- Safety Flash
- Published on 1 November 2022
- Generated on 24 April 2025
- IMCA SF 24/22
- 2 minute read
Jump to:
A member reports a significant increase in the number of dropped objects at third-party premises.
What happened?
The dropped object incidents have included many high potential near miss dropped objects which under different circumstances could have resulted in debilitating personal injuries. The dropped objects have been all manner of items, from heavy pipes, rigging failures through to nuts and bolts, that all had the potential for personal injury.
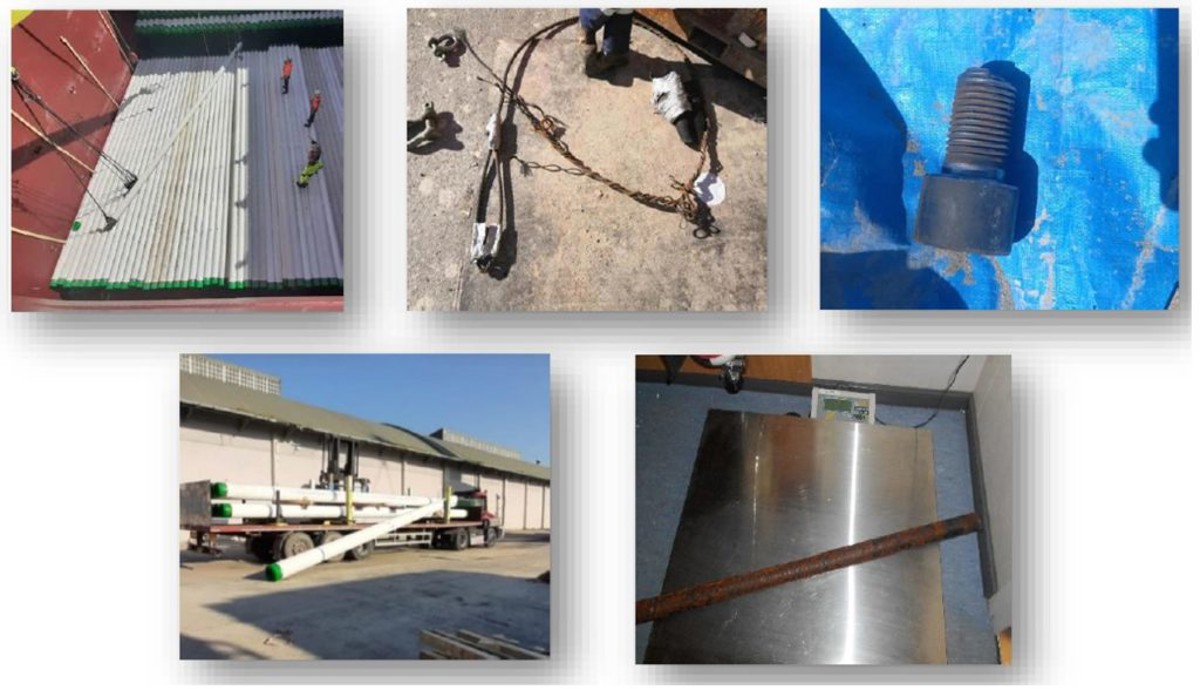
Examples include:
- Rigging failures.
- Weld Failures.
- Overhead gantry crane failures.
- Dropped pipe during pipe handling.
- Snagged rigging during pipe transfer.
- Incorrectly secured rigging.
What were the causes?
The following findings were identified from the third-party dropped object incidents, which were made a focus of learning, avoidance, and mitigation strategies to prevent future dropped objects:
- Inadequate procedural control that did not identify the correct process and risk management to be followed during pipe handling.
- Inadequate acknowledgement, adherence, understanding and assessment of risk controls in the risk assessments – truck inspections, banksmen/additional spotters not positioned correctly, toolbox talks not identifying the hazardous activities.
- Certifications of lifting equipment not adequate for expected use case.
- Incorrect equipment being used for transferring pipe.
- Human factors, risk perception and competency of personnel involved in operations.
- Inadequate quality control and inspection.
- Inadequate planned maintenance systems in place.
Our member reminded crew what to do:
- During the contracting process ensure that third-party HSE Management Systems (HSEMS) have fit for purpose risk controls in place to prevent/mitigate dropped objects.
- Set clear expectations with third-party contractors in respect of lifting and pipe handling activities.
- Formal understanding of differences between company and third-party contractors’ levels of oversight, mode of control and accountabilities – BEFORE starting work.
- Audits, inspections, and verifications of third-party operations to ensure that proper risk management controls are in place to prevent dropped objects;
- Ensure third parties consider and align with industry good practice.
- Remember the “7T’s” – Take The Time To Think Things Through.
- Support third-party contractors to ensure a focus on risk perception and considering regular “fresh eyes” reviews of work tasks and equipment use.
- On all worksites ensure that the obligation and expectation to exercise the stop work authority is clearly communicated and understood by all parties.
Related safety flashes
-
IMCA SF 32/21
25 November 2021
-
-
IMCA SF 10/15
16 July 2015
IMCA Safety Flashes summarise key safety matters and incidents, allowing lessons to be more easily learnt for the benefit of the entire offshore industry.
The effectiveness of the IMCA Safety Flash system depends on the industry sharing information and so avoiding repeat incidents. Incidents are classified according to IOGP's Life Saving Rules.
All information is anonymised or sanitised, as appropriate, and warnings for graphic content included where possible.
IMCA makes every effort to ensure both the accuracy and reliability of the information shared, but is not be liable for any guidance and/or recommendation and/or statement herein contained.
The information contained in this document does not fulfil or replace any individual's or Member's legal, regulatory or other duties or obligations in respect of their operations. Individuals and Members remain solely responsible for the safe, lawful and proper conduct of their operations.
Share your safety incidents with IMCA online. Sign-up to receive Safety Flashes straight to your email.