High potential near miss: failure of valve on gas bottle
- Safety Flash
- Published on 11 August 2017
- Generated on 27 April 2025
- IMCA SF 20/17
- 4 minute read
Jump to:
What happened?
The Royal New Zealand Navy has reported an explosion during the refilling of gas bottles used for naval diving operations. A crewman was refilling bottles when he heard a loud explosion and looked up to see the charging whip thrashing around violently. Upon establishing that it was safe to do so, the crewman closed all gas supply and receiver valves. After confirming that the situation had been stabilised, he reported the situation to his supervisor.
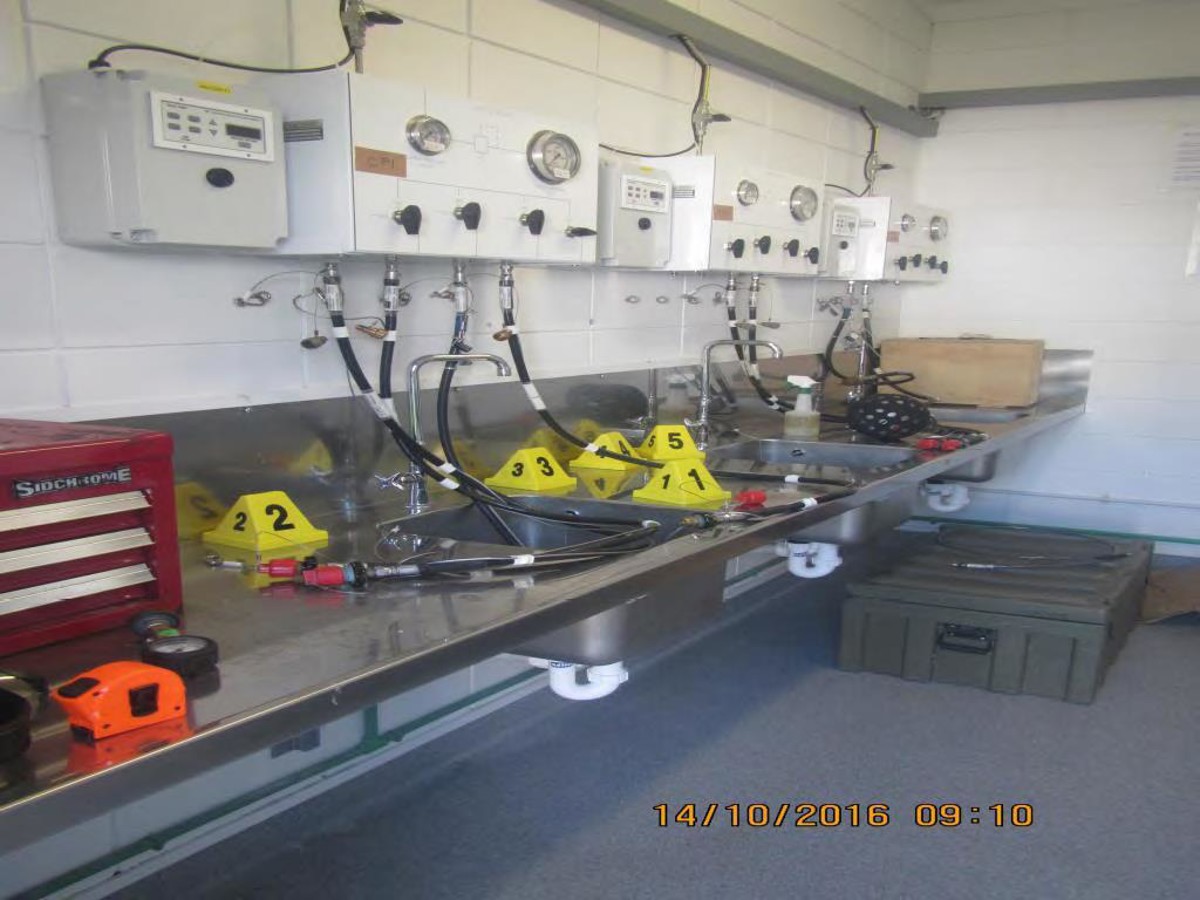
Though the filling components had been correctly connected, one of the bottle valves has failed and was violently expelled from the high pressure (HP) cylinder. As a result of the failure, the charging whip and valve remnant had forcefully impacted a nearby wall. Had these parts hit the crewman the consequences could have been very much more serious.
Swipe to see next image
What went wrong? What were the causes?
- The valve failure was mechanical in nature; a metallurgical failure of the integrity of the valve assembly, rather than being due to the process of filling the flask. Analysis determined that a combination of corrosion induced cracking and fatigue in the dipper tube thread roots lay at the heart of the failure.
- The exact cause of the corrosion could not be identified; however, the presence of dezincification and small particles of Verdigris in the cracks suggested that insufficient rinsing, after the 24-monthly application of mildly acidic BIOX cleaning compound, was the most probable cause.
- The level of Verdigris and the lack of oxygen caps and written emergency procedures show a need for further development of management systems.
- There was a post incident procedural failure, in that the person involved was not checked by a medic. Despite this he does not appear to have suffered any lasting detrimental effects as a result of the incident.
The following points, not strictly causal factors, were also identified by the investigation:
- While there can be statutory obligations relating to the testing and inspecting of cylinders, no such rules apply to the valves fitted to them.
- The lack of an appropriately defined operational life for valves of this nature (manufactured of non-magnetic brass vs. more conventional/durable materials) potentially missed an opportunity for them to have been ‘retired’ prior the failure.
- Oversights in regulatory compliance around correctly permanently marking or labelling valves.
- Lack of regulatory compliance in relation to ensuring that personnel involved in filling high pressure cylinders should hold appropriate (locally required) certification.
- Potential ‘oxygen cleanliness’ issues in relation to adherence to the fitting of valve caps when cylinders are not in use and limited the permissible levels of Verdigris build up on valve threads.
What actions were taken? What were the lessons learned?
- All similar valves of a similar age have been removed from service and replaced with new.
- Appropriate record-keeping measures were put in place for controlling the age of valves in use.
- A new method of securing filling arrester whips to cylinder necks was devised to prevent the potential thrashing around of loose whips under pressure.
- A review was made of procedures for valve oxygen cleanliness to ensure they meet the minimum internationally recommended standards.
- Recommendation was made that local regulations associated with the acquisition, introduction into service, on-going maintenance, marking and establishing a defined maximum operational life of valves used in association with HP cylinders, should be amended to reflect the lessons identified in this incident.
- Consider further development of training course for persons involved in filling HP cylinders.
Failure of gas bottle valves is unfortunately not uncommon. Members may wish to look through IMCA safety flashes themselves on our website:
Related Safety Flashes
-
IMCA SF 05/17
3 March 2017
-
-
IMCA SF 01/16
7 January 2016
-
IMCA SF 12/09
17 August 2009
IMCA Safety Flashes summarise key safety matters and incidents, allowing lessons to be more easily learnt for the benefit of the entire offshore industry.
The effectiveness of the IMCA Safety Flash system depends on the industry sharing information and so avoiding repeat incidents. Incidents are classified according to IOGP's Life Saving Rules.
All information is anonymised or sanitised, as appropriate, and warnings for graphic content included where possible.
IMCA makes every effort to ensure both the accuracy and reliability of the information shared, but is not be liable for any guidance and/or recommendation and/or statement herein contained.
The information contained in this document does not fulfil or replace any individual's or Member's legal, regulatory or other duties or obligations in respect of their operations. Individuals and Members remain solely responsible for the safe, lawful and proper conduct of their operations.
Share your safety incidents with IMCA online. Sign-up to receive Safety Flashes straight to your email.