Fatality during lifting operations
- Safety Flash
- Published on 2 December 2002
- Generated on 25 April 2025
- IMCA SF 11/02
- 4 minute read
Jump to:
IMCA has been advised of the following fatality which occurred on the pipe deck of an offshore platform.
What happened?
Two chemical pods had been stacked to make room for arriving cargo. To improve overall deck safety, it was decided to unstack the pods during the next shift, since all cargo had arrived and space was available. As this was a ‘blind’ lift, the crew included two flagmen/hookmen.
One of the hookmen climbed up the integrated ladder on the side of the pods, in order to hook the chain sling. During this operation, the crane pendant was lowered too much and went inside the frame holding the pod. When the hookman told the crane driver to lift up approximately 20cm, the pendant snagged the frame and lifted one end of the pod. As soon as one side of the tank had cleared the stacking lugs, the tank started to slide.
The hookman had his upper body above the frame and, when the tank toppled, his chest was crushed between the falling pod and an adjacent container, stored approximately 2.6 metres from the pods. The injuries to his chest were fatal and death was immediate.
What were the causes?
The company, in its investigations, noted that the deck had been surveyed by the crane driver prior to handover and that the deck had very well organised and managed. However, it noted the following points which had contributed to this incident:
- Inadequate design: the pods were designed for stacking, but the lugs did not properly prevent sliding if subject to external forces (e.g. crane, container). The chain slings were also too short to allow hooking from deck level, which had been required in the company’s procedure for stacking to be allowed.
- Inadequate planning and worksite walk-through: the safest way to perform the task had not been identified (the chain sling was hanging down the opposite side and there was no need to climb on top of the pod).
- Inadequate identification of job hazards: working at heights (4.6 metres at the top of the upper pod) and not recognising the potential hazard of a trapped pendant.
- Inadequate communication: the flagman could not see the top of the tank and hence could not direct the lowering of the crane pendant; the hookman was carrying out multiple tasks, including communication with the crane driver.
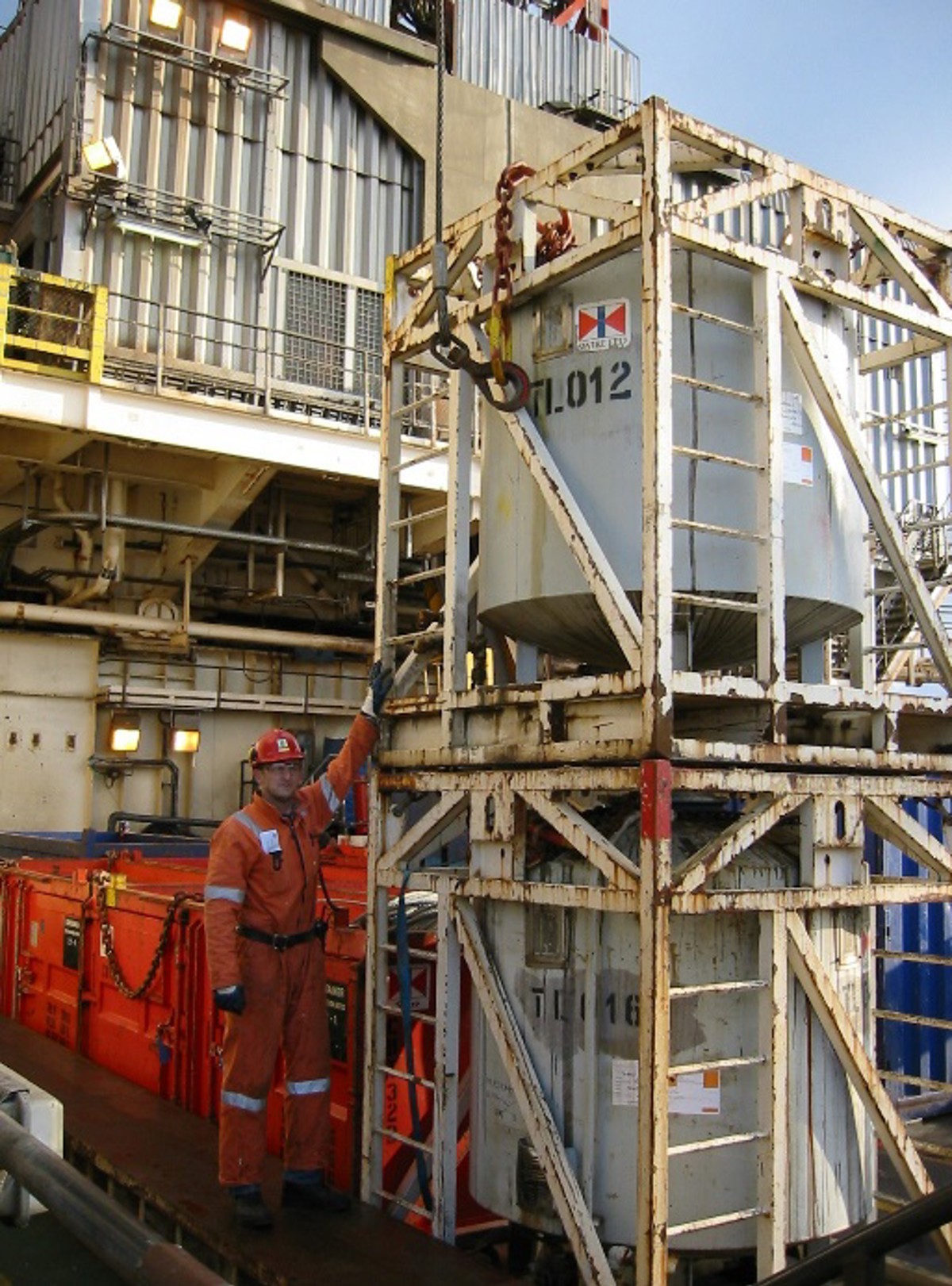
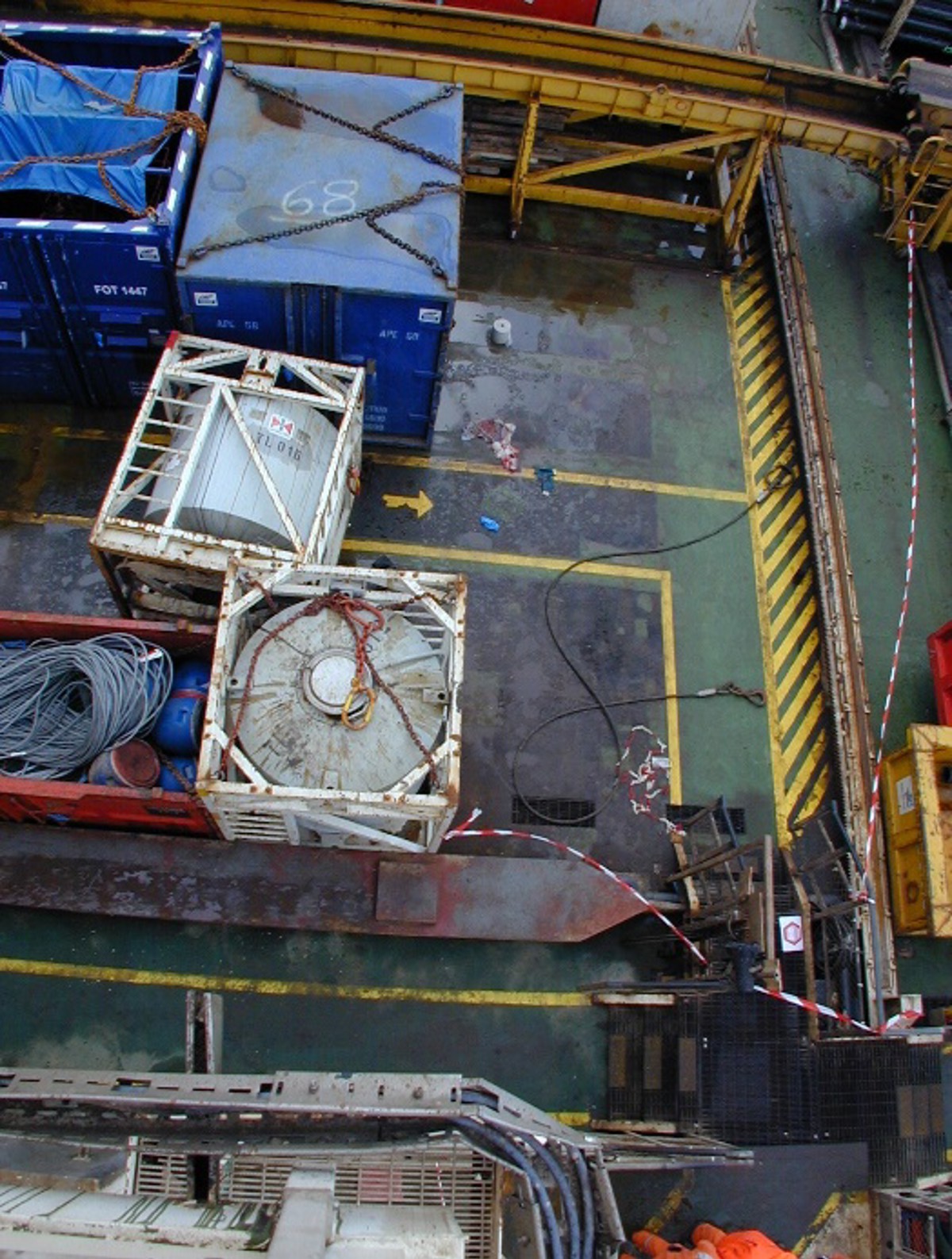
Lessons learnt
The investigation resulted in the following recommendations being made:
- Stacking of these pods and others of similar design to be banned by the company; consideration to be given to banning all stacking of containers.
- A pocket-sized aide-mémoire card to be introduced by the company, to prompt and aid appropriate prior assessment of lifts.
- Existing company rules on working at heights to be properly enforced (working on a ladder above 2 m height was already a violation of company rules).
- Company rules on lifting to be clarified/changed:
-
- ‘hooking at deck level’ means standing on the deck itself.
- flagman to be the only person communicating with the crane drive; flagman not to touch load; flagman to be identifiable by wearing a bright vest.
- ‘hooking at deck level’ means standing on the deck itself.
The company has also stressed the following points to its employees:
- Design standards for stackable containers are to be clear; suitable design should be checked.
- Stacking loads where people have to work is inherently dangerous – check if it’s happening on your worksite and review whether or not it should continue.
- Lifting operations, while often routine activities, are inherently dangerous with people around – check that people are adequately separated from the hazard; review how to recognise when a lift becomes non-routine.
- Working at height above 2m without adequate controls/safeguards in place is against company policy (‘prohibited’) – check it’s not happening on your worksite.
- Flagmen/banksmen should never be put in a position to handle a load – check that they’re not on your worksite.
- ‘Safety must be 100%. Be intolerant, small deviations will eventually combine and hurt you’.
IMCA Safety Flashes summarise key safety matters and incidents, allowing lessons to be more easily learnt for the benefit of the entire offshore industry.
The effectiveness of the IMCA Safety Flash system depends on the industry sharing information and so avoiding repeat incidents. Incidents are classified according to IOGP's Life Saving Rules.
All information is anonymised or sanitised, as appropriate, and warnings for graphic content included where possible.
IMCA makes every effort to ensure both the accuracy and reliability of the information shared, but is not be liable for any guidance and/or recommendation and/or statement herein contained.
The information contained in this document does not fulfil or replace any individual's or Member's legal, regulatory or other duties or obligations in respect of their operations. Individuals and Members remain solely responsible for the safe, lawful and proper conduct of their operations.
Share your safety incidents with IMCA online. Sign-up to receive Safety Flashes straight to your email.