High potential: electric shock near miss
- Safety Flash
- Published on 20 June 2022
- Generated on 30 June 2025
- IMCA SF 15/22
- 4 minute read
Jump to:
An engineer suffered a minor electrical shock while troubleshooting a faulty 690V electric motor.
What happened?
The engineer checked the drive belt and then proceeded to measure the phases. Measuring the phases was not in his initial plan when he prepared the troubleshooting. The incident occurred when he was measuring the phases.
The electric motor junction box cover was removed, and access to the wiring was good. Measurement was carried out using a multimeter. When he was about to replace the cover of the junction box, it touched one of the three phases and he suffered a minor electrical shock in his fingers. He was uninjured but had himself checked by the medic who confirmed this.
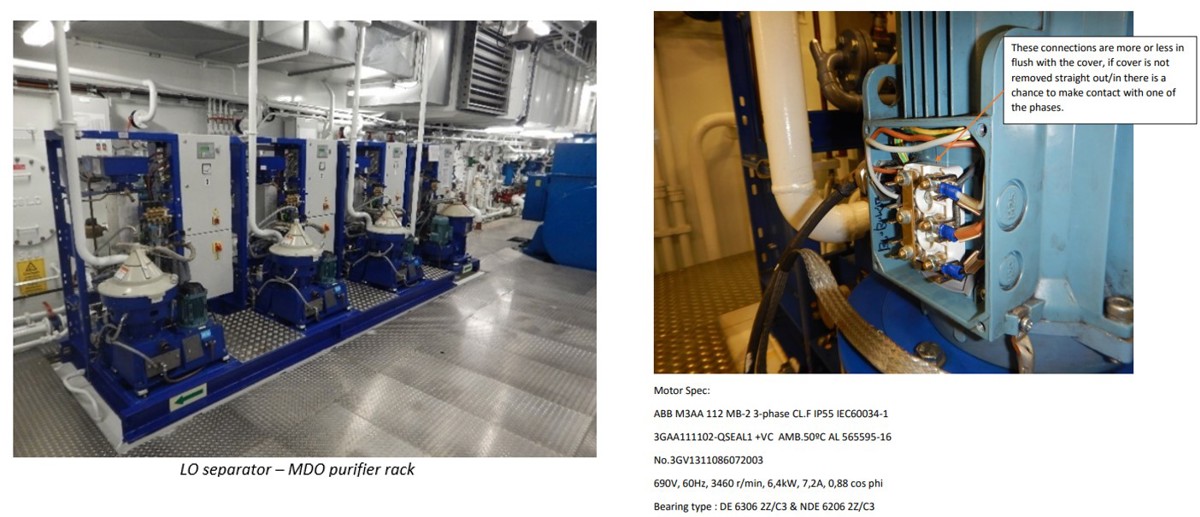
What went right?
- The engineer was competent to work with electrical components and this MDO purifier was one of the components assigned to him for investigation/check/maintenance.
- He was systematic in his troubleshooting and had already checked several other “usual” problems (e.g. water supply, timer to coils of water etc/ref. MDO purifier manual and previous “known issues”). Since these were all found ok, he asked the Chief Engineer for further advice. The Chief Engineer suggested he check the drive belt and shaft. This was a task which did not require any Permit to Work nor Lock Out/Tag Out.
- External factors like wind, sea state, vessel movements, illumination, slippery floor etc. were not contributing factors to the event.
What went wrong?
- The engineer decided on his own, without discussing with anyone else, to proceed and measure the phases on a live electric motor without a Permit to Work nor Lock Out/Tag Out in place.
- He was wearing safety/rubber boots, coverall and safety glasses but not approved gloves.
What was the cause?
- Failure to manage change: the engineer moved from doing a task which did not require PTW and LOTO, to a task that did. Had he stopped the job and correctly assessed the risk, it is likely that safety barriers would have been in place and risks mitigated.
- Energy Isolation: he did not identify the energy source and did not isolate it when the cover to the connection box was taken off and on. This resulted in him working on live equipment without proper PPE.
- Work Authorization: he did not identify that a Permit to Work was required before measurement of the phases. In addition, this task was not a part of the original plan and was not discussed with anyone.
Lessons learned
- Our member considered the potential for this incident to be major. This was because:
- The engineer was working on a live electrical system with 690V.
- The engineer did not use the appropriate gloves required for electrical work.
- if he had a knee or another body part in contact with a railing, the outcome could have been a serious injury or in worst case a fatality.
- If the junction box cover had touched two phases, the result would have been an arc (explosion), resulting in potential burns.
- This incident happened when routine work was being carried out. Work that was initially low risk, became a high risk task when the engineer included troubleshooting/measuring phases on the electrical motor. He did not carry out a thorough risk assessment of the situation and did not complete required documents.
- Whist we all want to solve the problem and get the job done, we should never jeopardize our own health or safety by ignoring precautions set by our company’s policies, procedures and checklists.
Our member made the following changes:
- To avoid similar incidents in the future, it was agreed that no job be started before all necessary safety precautions have been discussed by a minimum of two crew members from engine department (any job, even if Permit To Work is not required).
- The company implemented the IOGP’s Live-saving rules. These statements simplify the important questions personnel need to ask themselves before starting work.
Related Safety Flashes
-
IMCA SF 05/22
28 February 2022
-
-
IMCA SF 26/21
22 September 2021
-
-
IMCA SF 06/20
19 February 2020
-
-
IMCA SF 15/18
20 July 2018
IMCA Safety Flashes summarise key safety matters and incidents, allowing lessons to be more easily learnt for the benefit of the entire offshore industry.
The effectiveness of the IMCA Safety Flash system depends on the industry sharing information and so avoiding repeat incidents. Incidents are classified according to IOGP's Life Saving Rules.
All information is anonymised or sanitised, as appropriate, and warnings for graphic content included where possible.
IMCA makes every effort to ensure both the accuracy and reliability of the information shared, but is not be liable for any guidance and/or recommendation and/or statement herein contained.
The information contained in this document does not fulfil or replace any individual's or Member's legal, regulatory or other duties or obligations in respect of their operations. Individuals and Members remain solely responsible for the safe, lawful and proper conduct of their operations.
Share your safety incidents with IMCA online. Sign-up to receive Safety Flashes straight to your email.