Differential pressure: Dummy choke ejected close to divers
- Safety Flash
- Published on 16 May 2023
- Generated on 13 July 2025
- IMCA SF 12/23
- 3 minute read
Jump to:
A dummy choke insert was ejected from a water injection (WI) tree by force of differential pressure, while two divers were working nearby.
What happened?
A dive team was removing a dummy choke insert and replacing it with a choke valve insert. The WI tree had been subject to hydrate remediation works. With no hydrates evident, limited trapped or pressurised gas was expected and tested barriers and isolations were in place.
During the removal of the half shell clamps that retained the dummy choke insert, unexpected differential pressure from the flowline forced the dummy choke insert (85 kg in water) out of the choke valve body at significant force.
The two divers were loosening the clamp bolts around the dummy choke and were therefore close by when it ejected. Neither diver was in the direct line of fire; both were unharmed.
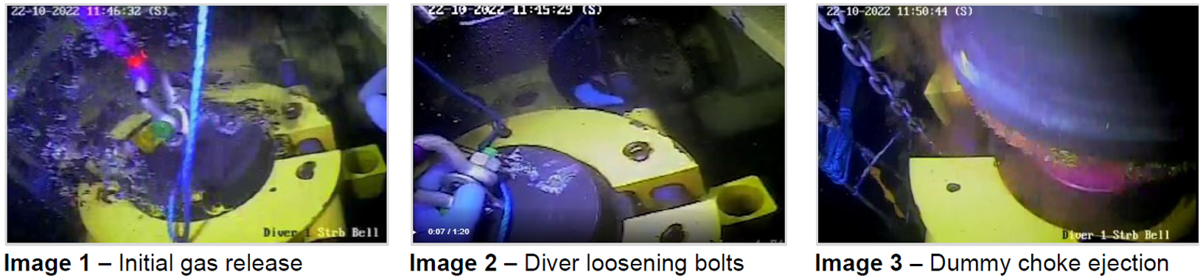
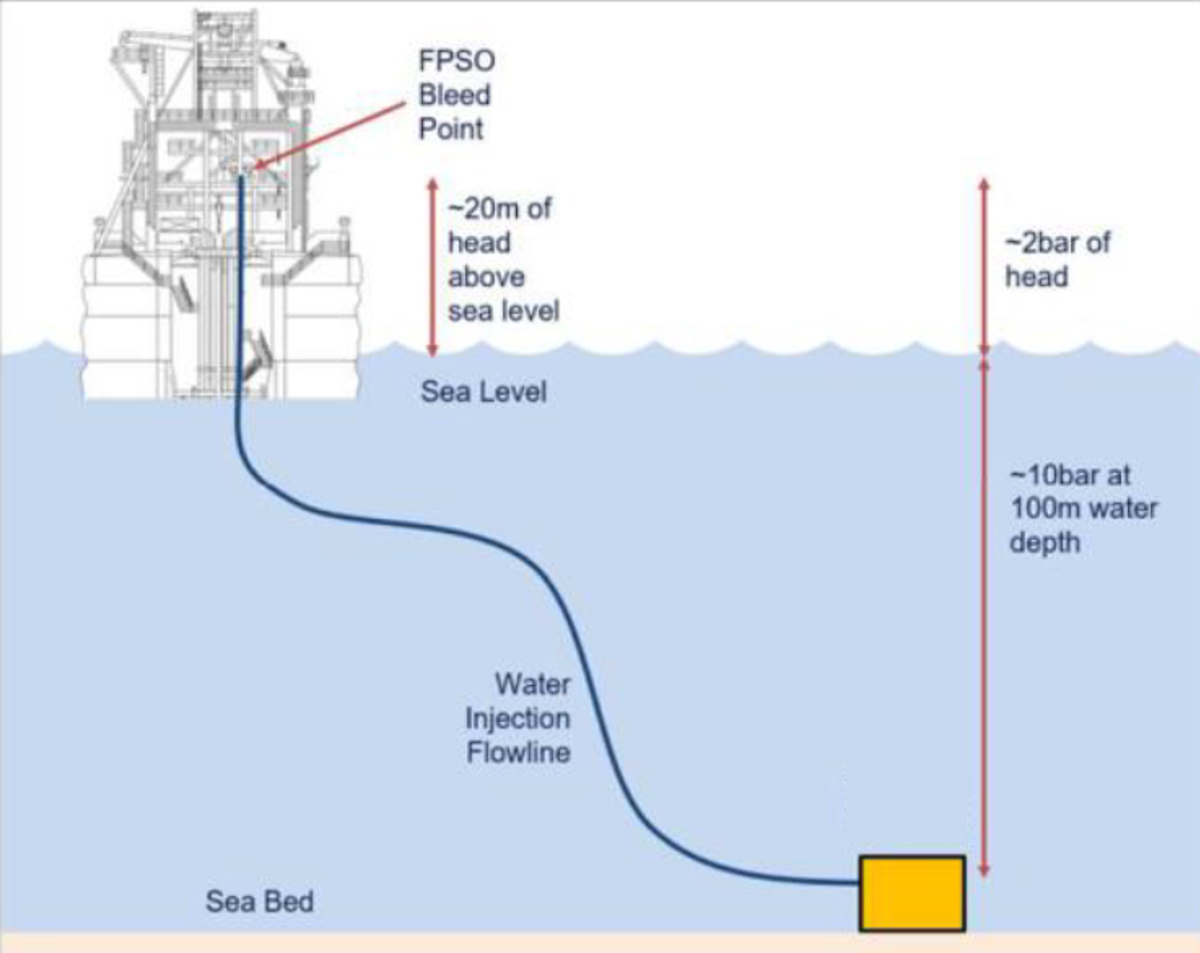
What went wrong?
- During the design of the dummy choke insert, the decision was made not to include a test port, which would have allowed venting of any pressure built up in the flowline. The port was not part of the supplier’s standard design, and there was not enough time to approve a design change to include the port.
- The project procedure instructed that the Subsea Pressure and Monitoring Manifold (SPAMM) should be left closed, so there was no local vent path from the flowline.
- When pressure differentials in the system were noted prior to the dummy choke removal, there was no recognition that readings were not as expected, and no discussions within the team relating to venting off the remaining pressure.
- Based on previous experience at the tree, gas/fluid release had been identified as a hazard in the procedure and in the Hazard Identification and Risk Assessment (HIRA) - however, no parameters had been set as to the expected volume or duration of the release.
- Divers continued to work to loosen the clamp while gas/fluid was escaping from the choke, as the team had assumed that previous venting had been successful, and that they were safe to proceed.
- Our Member notes that “the key point throughout was the failure to understand the exact pressure within the flowline, which was the residual 2 bar head of pressure from the riser after Floating Production Storage and Offloading (FPSO) venting”.
Actions
- Design safety in at the early engineering phase of a project – in this case, inclusion of a test port.
- Ensure procedures and risk assessments are clear, unambiguous, and explicit in their requirements (rather than leaving things vague, ambiguous and implicit). This is particularly important when dealing with a pressurised system and/or with stored energy.
- When using subsea pressure gauges, ensure any reading anomalies are well understood, communicated to the full team, and recorded. If the gauge is behaving in an anomalous way, swap it out.
- When ‘line of fire’ or ‘stored energy’ is identified as a hazard, ensure that control measures are specific in how these hazards will be managed so that personnel are in a safe position. Relevant control measures may include: hard barriers, safe havens, extended hand tools or use of rigging.
- When carrying out diver intervention works involving barriers and isolations, ensure all relevant parties have had comprehensive training in isolations and barriers.
- Divers and Dive Supervisors should confirm a local vent is open before starting any work on pressurised systems.
- If any step in a procedure doesn’t look right (e.g., local vent to be left closed when working on a pressurised system), STOP the JOB: Call an all stop and seek clarification.
Related safety flashes
-
IMCA SF 03/17
13 February 2017
-
-
IMCA SF 20/16
2 August 2016
-
IMCA SF 14/11
23 December 2011
IMCA Safety Flashes summarise key safety matters and incidents, allowing lessons to be more easily learnt for the benefit of the entire offshore industry.
The effectiveness of the IMCA Safety Flash system depends on the industry sharing information and so avoiding repeat incidents. Incidents are classified according to IOGP's Life Saving Rules.
All information is anonymised or sanitised, as appropriate, and warnings for graphic content included where possible.
IMCA makes every effort to ensure both the accuracy and reliability of the information shared, but is not be liable for any guidance and/or recommendation and/or statement herein contained.
The information contained in this document does not fulfil or replace any individual's or Member's legal, regulatory or other duties or obligations in respect of their operations. Individuals and Members remain solely responsible for the safe, lawful and proper conduct of their operations.
Share your safety incidents with IMCA online. Sign-up to receive Safety Flashes straight to your email.