Near miss: Vessel approach to wind turbine tower
- Safety Flash
- Published on 8 April 2021
- Generated on 9 July 2025
- IMCA SF 10/21
- 4 minute read
Jump to:
A Member reports two near miss incidents within two weeks of one another, in which during the approach of a vessel to a wind turbine tower, the nacelle started moving, with the risk of the vessel being hit or gangway being knocked off by the wind turbine blades. No harm was done in either incident.
The incidents occurred during the use of walk-to-work vessels for shipping and transferring personnel to and from wind turbine towers offshore, a procedure that occurs frequently every day, requiring close co-operation between bridge crew and the client’s personnel. No harm was done in either incident.
The turbine blades at this particular wind farm reach to within 23 m of sea level at their lowest point. Thus, when the blades or the nacelle are turning, a ship within the turbine’s safety zone could be struck. Therefore, safe docking and transfer of personnel requires a total STOP of the turbine. In STOP mode, the electric system is switched off, preventing any movement of the nacelle and/or the blades.
What happened – Incident 1
A vessel approached a turbine to carry out transfer of personnel and cargo. Before the approach, the responsible person on the turbine tower used software control to lock the nacelle at a safe heading, and communicated this to the vessel bridge. Personnel had just been transferred by the gangway to the turbine, when the vessel crane operator noticed that the nacelle heading was changing. This was also observed by the bridge team. The lower blade was very close to the forward part of the vessel. The vessel, in emergency mode, immediately moved out to a safe distance of 100m and the client was informed.
What happened – Incident 2
This was a similar situation less than one month later. There was a yawing turbine during docking. The turbine had stopped automatically because of a software error. The arriving crew initially reset the alarms before putting the turbine in STOP mode manually. However, directly after the reset, the turbine went to autonomous mode and started yawing before the vessel had moved out to the safe zone. The imminent danger was that the vessel could have been hit by the blades, which fortunately did not happen.
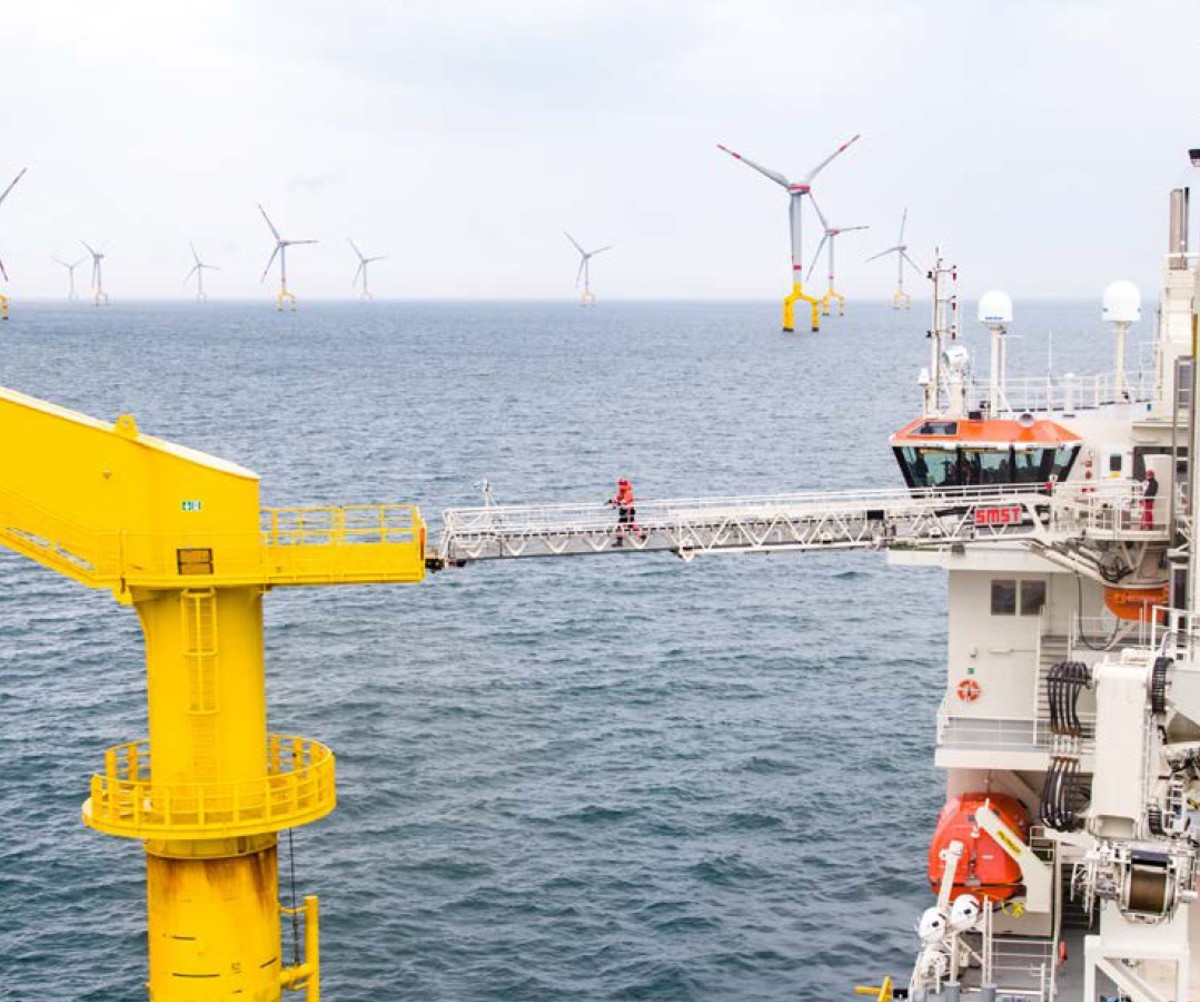
Transferring from vessel to turbine
What went wrong?
Investigations by the crew directly after the first incident event disclosed that the responsible person, working the software onboard the vessel, had not put the turbine in full STOP mode, but inadvertently put it in autonomous mode. It was suggested that the responsible person “seemed a bit pressed that morning”, causing him to forget to click the (second) tickbox in the software to not only put the turbine in autonomous mode but also in STOP-mode.
In addition, the turbine’s internal cables were at maximum twisted status, which occurs after a turbine has wound the maximum of 5 turns around the tower. A turbine in autonomous mode will automatically start yawing to unwind the cables. This was the initial cause of the near miss.
What were the causes?
Our Member’s investigation and analysis of these incidents revealed the following direct causes:
- Danger and risk were inadequately identified. The root cause our member identified was human error.
- The warning systems in place were inadequate. The control software gave no warning about the turbine generator electrical system not being in STOP mode, and the bridge crew were unable to verify this, so the vessel started to approach.
- Procedures and instructions were inadequate.
- The details of vessel approach and the subsequent steps of the turbine electrical STOP procedure were not discussed in project preparation.
- It was not identified that the responsible person was in effect working alone and that there was no means of verifying the reponsible person’s work or actions.
- In addition, there was insufficient communication between client and contractor and insufficient understanding of each other’s procedures. The procedures for approach and necessary turbine electrical system STOP of the wind turbine generator were not discussed thoroughly during kick-off nor in daily toolbox talks.
- The details of vessel approach and the subsequent steps of the turbine electrical STOP procedure were not discussed in project preparation.
The vessel was prevented from being hit by the turbine blades by the quick reaction of the bridge personnel. After the turbine was put into STOP mode correctly, the vessel made a second, successful approach without further incident.
Members may wish to refer to:
- IMCA M254 Guidelines for Walk to Work Operations
- IMCA HSS025 Guidance on the transfer of personnel to and from offshore vessels and structures
IMCA Safety Flashes summarise key safety matters and incidents, allowing lessons to be more easily learnt for the benefit of the entire offshore industry.
The effectiveness of the IMCA Safety Flash system depends on the industry sharing information and so avoiding repeat incidents. Incidents are classified according to IOGP's Life Saving Rules.
All information is anonymised or sanitised, as appropriate, and warnings for graphic content included where possible.
IMCA makes every effort to ensure both the accuracy and reliability of the information shared, but is not be liable for any guidance and/or recommendation and/or statement herein contained.
The information contained in this document does not fulfil or replace any individual's or Member's legal, regulatory or other duties or obligations in respect of their operations. Individuals and Members remain solely responsible for the safe, lawful and proper conduct of their operations.
Share your safety incidents with IMCA online. Sign-up to receive Safety Flashes straight to your email.