Riggers struck/trapped by pipe section
- Safety Flash
- Published on 8 April 2022
- Generated on 2 July 2025
- IMCA SF 09/22
- 4 minute read
Jump to:
A pipe section being lowered into position unexpectedly moved sideways, striking two riggers.
What happened?
A vessel crane was lifting two 16 inch pipes of 24.4m length from a supply vessel to the pipelayer conveyor system. The second pipe section when being lowered into position unexpectedly moved sideways, striking two riggers, and trapping one between the suspended pipe and the vessel handrail. The rigger caught between the load and the handrail suffered a fracture in his back. Of the two who were struck, one suffered bruising to the ribs, and the other was physically unharmed.
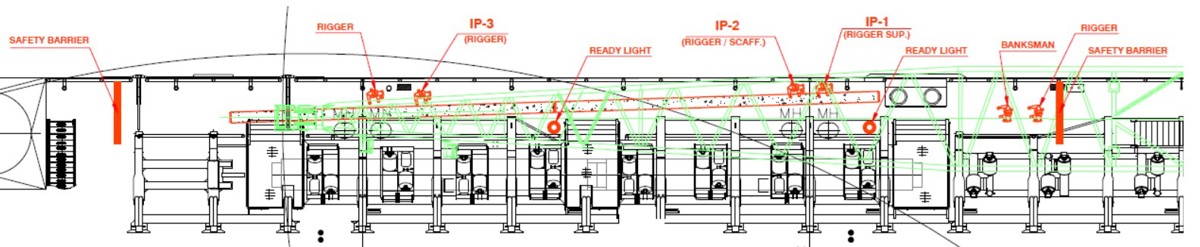
What happened? (cont.)
It was an established practice to lift two pipes at a time from the supply vessel, stabilize them against the conveyor bumper bars, then lower both pipes onto the conveyor. Riggers then step forward and disconnect one pipe from the crane, leaving the second pipe connected. The riggers then remove the end caps, soft slings, and rope rings from the first pipe. The second pipe is then raised, still resting against the bumper bars and the first pipe is transferred along the conveyor into the firing line. Once the first pipe has moved into the firing line, the second pipe is then lowered into the conveyor and the riggers repeat the preparation process. The riggers are expected to vacate the immediate area while the second pipe is raised and lowered.
On instruction from the banksman to lower the second pipe, it moved downward and away from the bumper bars. The pipe continued its horizonal motion, striking three riggers who were standing between the conveyor rollers and the vessel handrail. One rigger received a glancing blow. One rigger was momentarily impacted, and one rigger was caught between the suspended pipe and the handrail.
What went wrong?
Our members’ findings indicated that:
- The crane operator did not follow the banksman’s instruction to lower but also introduced slew. The crane operator was new to the project crane operator position and this change in workload may have been a stressor.
- The rigging supervisor was directly involved in removing load rigging and protection and not in a stand-off position to oversee operations.
- No-one stopped the job: neither the banksman, supervisor nor crane operator, stopped the operation to ensure the line of fire zone was clear.
- The riggers remained in the line of fire during the movement of the second pipe section.
- The requirement to get out of the way while the pipe was raised was not specified in the task plan or the task risk assessment (TRA) but was discussed at the toolbox talk. Conflict was introduced through a verbal requirement reinforced in the toolbox talk to keep clear, whereas the task plan required riggers to be near the pipe to remove taglines.
- The repetitive nature of the operation, without any issues being experienced, may have reduced the risk perception of the potential line of fire hazard, making the riggers positions appear safe to them.
Lessons learned
- Ensure that crane operation communications are clear, repeated and confirmed before load movements.
- Operations which have line of fire hazards should be checked to confirm the safe positioning of personnel is clearly defined, understood, and followed.
- Review zones where line of fire operations are regularly conducted. Confirm that where appropriate suitable barriers (permanent or temporary) are in place.
- Consider marking the deck as to identify no-go zones or restricted access.
- For repetitive work consider frequent toolbox talk sessions or introduce a pause to question the team to confirm they remain focused on the task and to reinforce the potential hazards and the controls to be maintained.
- Review repetitive high-risk tasks to confirm risk awareness is not decaying.
Related Safety Flashes
-
IMCA SF 09/19
3 May 2019
-
-
IMCA SF 04/15
20 March 2015
-
IMCA SF 11/02
2 December 2002
-
IMCA SF 16/09
10 November 2009
-
IMCA SF 18/13
20 December 2013
IMCA Safety Flashes summarise key safety matters and incidents, allowing lessons to be more easily learnt for the benefit of the entire offshore industry.
The effectiveness of the IMCA Safety Flash system depends on the industry sharing information and so avoiding repeat incidents. Incidents are classified according to IOGP's Life Saving Rules.
All information is anonymised or sanitised, as appropriate, and warnings for graphic content included where possible.
IMCA makes every effort to ensure both the accuracy and reliability of the information shared, but is not be liable for any guidance and/or recommendation and/or statement herein contained.
The information contained in this document does not fulfil or replace any individual's or Member's legal, regulatory or other duties or obligations in respect of their operations. Individuals and Members remain solely responsible for the safe, lawful and proper conduct of their operations.
Share your safety incidents with IMCA online. Sign-up to receive Safety Flashes straight to your email.