Fatality: Pressure build-up leading to sudden release of mechanical plug
- Safety Flash
- Published on 3 July 2003
- Generated on 3 May 2025
- IMCA SF 08/03
- 6 minute read
Jump to:
A Member has reported the following incident, whereby a mechanical plug installed inside a pipe to isolate hot work from process fluids released suddenly, striking and killing a welder.
What happened?
Results from the investigation indicate that the direct cause of the incident was blockage of the purge vent line on the back side of the plug due to freezing water vapour in the line. This allowed pressure to build up and eject the plug.
While freezing contributed to the blockage in this incident, it is not the only means by which pressure can build-up. Given the ‘routine’ use of these types of plugs in production operations, all relevant personnel should be made aware of the events in this incident and a review of isolation plug procedures is encouraged.
The work in this incident involved a welding operation on the open end of a 28-inch produced water line that had residual water and hydrocarbons in it. A non-pressure-containing mechanical plug, known as a ‘plumber’s plug’, had been installed about 12 inches inside the pipe, as a barrier against process fluids and purge gas. About three hours before the incident, a nitrogen purge was established through a fitting in the plug to inert the pipe area behind the plug. The nitrogen came from a nearby supply header operating at 25-30 psig. The purge gas was routed to the plug from the header via a ¾-inch flexible hose. Another ¾-inch hose was connected to the top of the pipe behind the plug and routed outside the module to vent the vapors. The ambient temperature was 0°F at the time of the incident. A hand valve was used to pinch the flow of purge gas from the nitrogen header. There was no pressure gauge, regulator, or secondary relief on the purge to allow pressure to be checked or to prevent pressure build-up. A job safety analysis (JSA) recognized the potential hazard of the purge line freezing. To mitigate the risk, the line was checked periodically for flow by placing a hand at the end of the vent hose. This check subsequently proved to be inadequate. When the vent line froze, the pressure build-up behind the plug caused the 63-pound plug to release suddenly, striking and killing the welder and inflicting minor injuries on two other workers.
The company involved has reported the following lessons learned:
The primary lesson learned is recognition of the risk associated with potential pressure build-up behind plugs that are not intended to hold pressure. When purging systems using such plugs, procedures should address the size of inlet and vent hoses, placement of vent hoses, use of regulators to control flow, use of secondary pressure relief to prevent overpressure, positioning of workers away from the plug, and work crew training and hazard awareness. Where possible, the best option is to design tie-ins so that isolation plugs between hot work and hydrocarbons are not needed. In addition to the ‘plumber’s plug’, the company involved is evaluating alternative plug types when isolation is needed. These alternatives include double-sealing hydraulic plugs (Car-Ber type) and pressure rated plugs (Thaxton) that have the potential to be used with or without purging.
The investigation report also identified potential issues with JSA and lesson learned processes at the work site. While the JSA had identified the vent freeze-up hazard, the risk had not been properly mitigated. In addition, the crew doing the work was not directly involved in the JSA. A similar near-miss occurred earlier in the year when a 4-inch plug blew out due to a malfunction of the pressure regulator on the purge gas. Lessons from that event did not get incorporated into existing procedures.
The company is reviewing its JSA and lesson learned processes as described below and has sought examples of best practices and lessons learned from its employees’ experiences with use of such plugs for wider sharing.
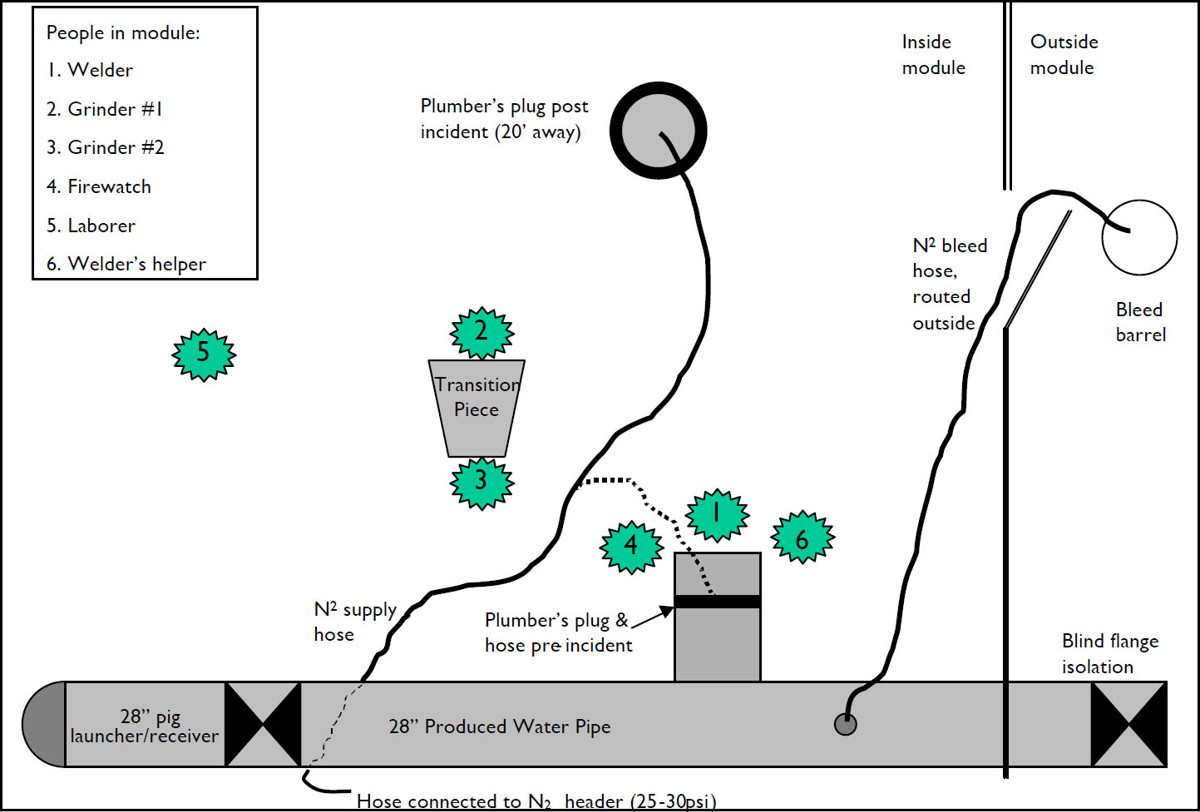
The company has provided the following summary of actions and lessons learned following the incident:
- Contractor workgroup formed.
- Rigorous review by engineering and operations staff of mechanical plugs, including specifications and design criteria.
- Evaluation of alternative technologies (Car-Ber) to potentially reduce or eliminate the need for nitrogen purges.
- Revise procedures accordingly.
- Hazard recognition addressed: Although the importance of monitoring the vent hose was known and noted in the hot work permit, no rigorous monitoring programme was used. Several hazards had not been identified during the JSA/STA process:
- The Nâ‚‚ would absorb the water left in the 28″ pipe;
- The absorbed water would condense and freeze in the vent hose;
- Very low pressure would exert large forces on a large diameter plug;
- A company standard is to be developed for hazard analysis for all work, including ‘routine’ jobs, on its work permit task hazard checklist, including JSAs, STAs, JHAs, SETA cards, unit work permits, task hazard checklists and authority to proceed.
- Effectiveness of lessons learned process reviewed:
- Learnings from an earlier near-miss (where a regulator had malfunctioned, leading to increased nitrogen pressure) had not been enough to prevent this incident;
- Although company procedures were updated periodically, relevant procedures are also to be reviewed whenever a report of lessons learned is issued. The company will use its own network to improve sharing of safety information among its global assets.
- Purging, cold cutting and welding on process piping procedure updated: . First choice to isolate piping so that a plug is not needed:
- Where a plug is needed, one not requiring the use of interting, such as a Car-Ber plug, is to be selected.
- If only a plug requiring an inert purge is needed, a job-specific procedure is to be prepared, addressing:
- the size and pressure rating of inlet and vent hoses.
- the placement of vent hoses (inside/outside).
- the use of low pressure gauges at the inlet of the plug and on the backside of the plug.
- the use of regulators and pressure relief.
- the positioning of workers away from mechanical plugs.
- training and work plans for the crew involved, including assigning a crew member to continuously monitor pressures and inert gas flow rate.
- Requirements to be clearly communicated through updated procedures.
- Re-emphasising the importance of being safety-aware at all times, including before and during ‘routine’ tasks:
- Think hard about the risks of every task undertaken – even ‘routine’ tasks!
- Don’t be complacent about risks, just because you’ve done a job lots of times
- Every welding job is unique – you must stop, think and go!
IMCA Safety Flashes summarise key safety matters and incidents, allowing lessons to be more easily learnt for the benefit of the entire offshore industry.
The effectiveness of the IMCA Safety Flash system depends on the industry sharing information and so avoiding repeat incidents. Incidents are classified according to IOGP's Life Saving Rules.
All information is anonymised or sanitised, as appropriate, and warnings for graphic content included where possible.
IMCA makes every effort to ensure both the accuracy and reliability of the information shared, but is not be liable for any guidance and/or recommendation and/or statement herein contained.
The information contained in this document does not fulfil or replace any individual's or Member's legal, regulatory or other duties or obligations in respect of their operations. Individuals and Members remain solely responsible for the safe, lawful and proper conduct of their operations.
Share your safety incidents with IMCA online. Sign-up to receive Safety Flashes straight to your email.