Dropped objects in dry dock
- Safety Flash
- Published on 9 February 2023
- Generated on 19 April 2025
- IMCA SF 04/23
- 4 minute read
Jump to:
A member reports two dropped object incidents during a vessel dry-dock, both with serious injury potential
Incident 1: What happened?
During a thruster overhaul, the hold-back rigging for the steering pipe failed and the pipe subsequently dropped to the dry dock bottom directly below the vessel keel.
An original equipment manufacturer (OEM) was contracted to oversee the removal of a thruster pod lower gearbox, drive shaft, telescopic tube, and steering tube to allow the steering tube bearings to be removed.
The rigging was installed and managed by the shipyard. To assist in the freeing of the tube the OEM lead decided to slacken the chain blocks about 18 cm to aid the release of the tube.
The shipyard team were unaware of this adjustment.
The OEM lead gave the shipyard team instruction to release the tube which caused the tube to drop 18 cm.
The slack in the chain blocks enabled a shock loading on the chain blocks causing the tube to slip and fall 1.8 metres to the dock bottom.
Incident 2: What happened?
A hydraulic cylinder clevis pin “cap” slid from the tower during workstation maintenance and fell 14 metres into the dry dock.
A team of technicians were working to remove a hydraulic cylinder on the workstation of the vessel tower.
To remove the cap, seized to the cylinder pin by rust, one of them used a hammer; the cap bounced outwards and fell 40 cm onto a platform below.
Due to the tower angle of 36° the cap then slid towards an uncovered gap and fell to the dock bottom.
A third-party work team were in the dock bottom near to where the dropped cap landed.
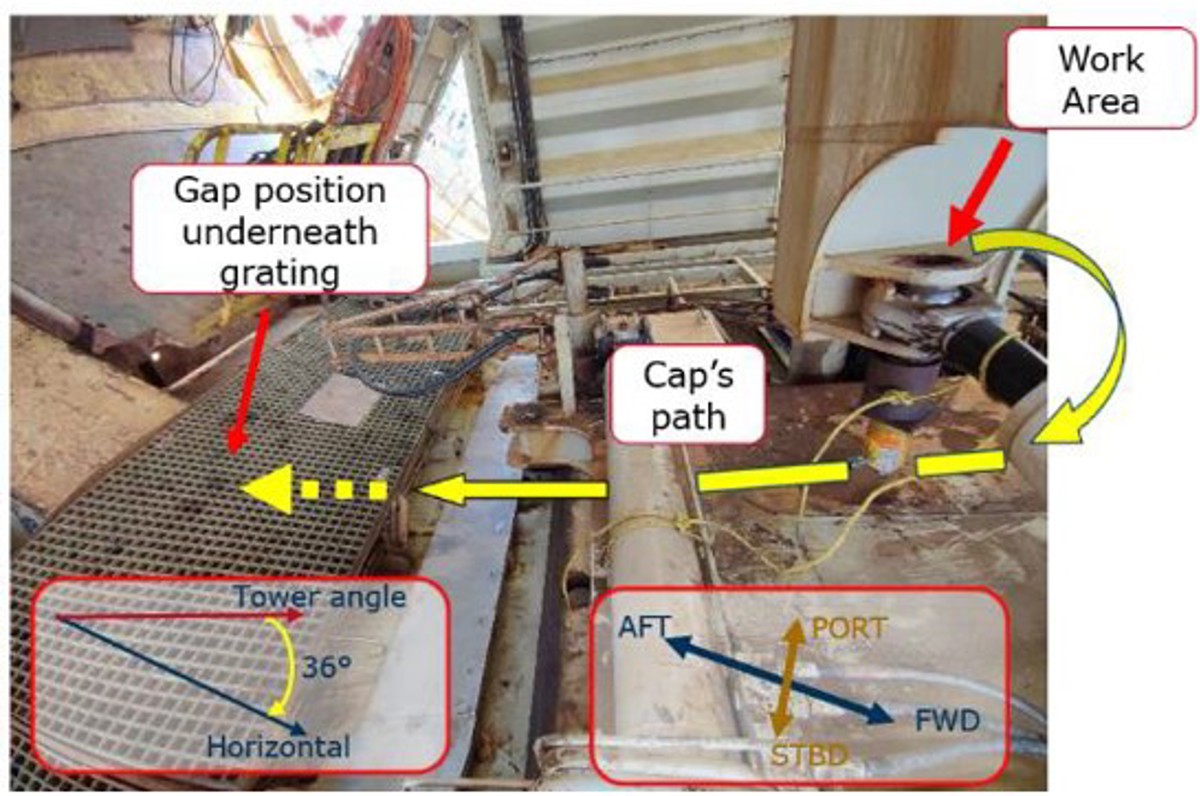
Path of 1.1 kg cylinder pin cap
What went wrong?
Findings
In both incidents, aspects of the work were not considered or assessed within Task Risk Assessments (TRAs), Permit to Work and Tool-Box Talk discussions. There was insufficient consideration of:
- changes occurring to the worksite
- crew working on different levels – this was not identified as presenting a DROPS risks
- third-party crew being allowed on the dock bottom without complete notification
- precautions specified in a permit to work not being followed
- the OEM personnel were working beyond agreed authority levels.
The activities in both incidents were subject to Safety Management System interface between the shipyard and the OEM. The dry dock project team and vessel management team were following the Control of Work process to manage these interfaces and determine the required controls and supervision to manage several simultaneous operations (SIMOPs). This is a common aspect of shipyard/dry dock activities.
Lessons learned
- Ensure appropriately controlled safety barriers are maintained to provide adequate protection and prevent an incident.
- Ensure pre-job planning and risk assessment is robust enough, detailed enough and specific enough for the task in hand, and that sufficient familiarisation time is allowed for those involved. Non-routine activities such as dry docks should be subject to greater focus on hazards and risks.
- Ensure and confirm that there are robust interface arrangements in place and understood between all the different parties in a dry dock or shipyard situation. This should include the yard, OEMs and third-party contractors, vessel management and project team.
- Ensure there are regular Control of Work meetings to communicate and control all activities at the site. These are a necessary and effective means to confirm the robustness and accuracy of the safety management system and ensure things are done safely.
- Ensure you know the procedures for the job you are doing. If you need to go through the procedure again with the team, take the time to do so. Check that everyone clearly understands their role and responsibility within the planned activity.
- Anyone in doubt should stop and take the time to think and talk it through with the team.
Members may wish to refer to:
- IMCA HSS032 Guidance on safety in shipyards
- IMCA M203 Guidance on simultaneous operations (SIMOPS)
Related safety flashes
-
IMCA SF 26/21
22 September 2021
-
-
IMCA SF 10/21
8 April 2021
-
-
IMCA SF 23/16
13 September 2016
IMCA Safety Flashes summarise key safety matters and incidents, allowing lessons to be more easily learnt for the benefit of the entire offshore industry.
The effectiveness of the IMCA Safety Flash system depends on the industry sharing information and so avoiding repeat incidents. Incidents are classified according to IOGP's Life Saving Rules.
All information is anonymised or sanitised, as appropriate, and warnings for graphic content included where possible.
IMCA makes every effort to ensure both the accuracy and reliability of the information shared, but is not be liable for any guidance and/or recommendation and/or statement herein contained.
The information contained in this document does not fulfil or replace any individual's or Member's legal, regulatory or other duties or obligations in respect of their operations. Individuals and Members remain solely responsible for the safe, lawful and proper conduct of their operations.
Share your safety incidents with IMCA online. Sign-up to receive Safety Flashes straight to your email.