Capstan wire parted during deployment of anchor buoy
- Safety Flash
- Published on 3 March 2015
- Generated on 22 February 2025
- IMCA SF 03/15
- 3 minute read
Jump to:
A member has reported an incident in which a wire parted whilst dragging an anchor buoy on deck.
The incident occurred when a vessel was involved in a Delta Flipper anchor drag test operation. The operation consisted of deployment one after the other, of an anchor buoy and a Delta Flipper type anchor, using two capstan wires, and then recovery back to deck using the main tow wire.
Three tests were carried out successfully. During the fourth test, the port side capstan wire parted whilst dragging the anchor buoy on deck. There were no injuries.
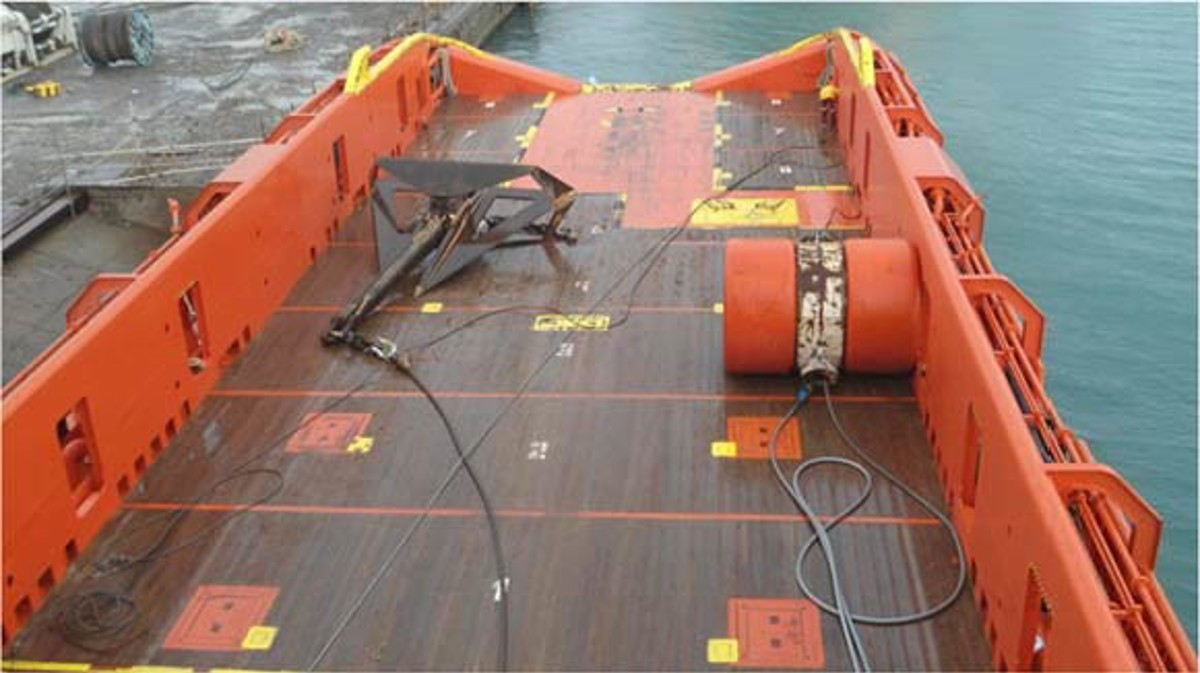
view of back deck showing Delta Flipper anchor (left), Anchor Buoy (right) and Capstan (arrow)
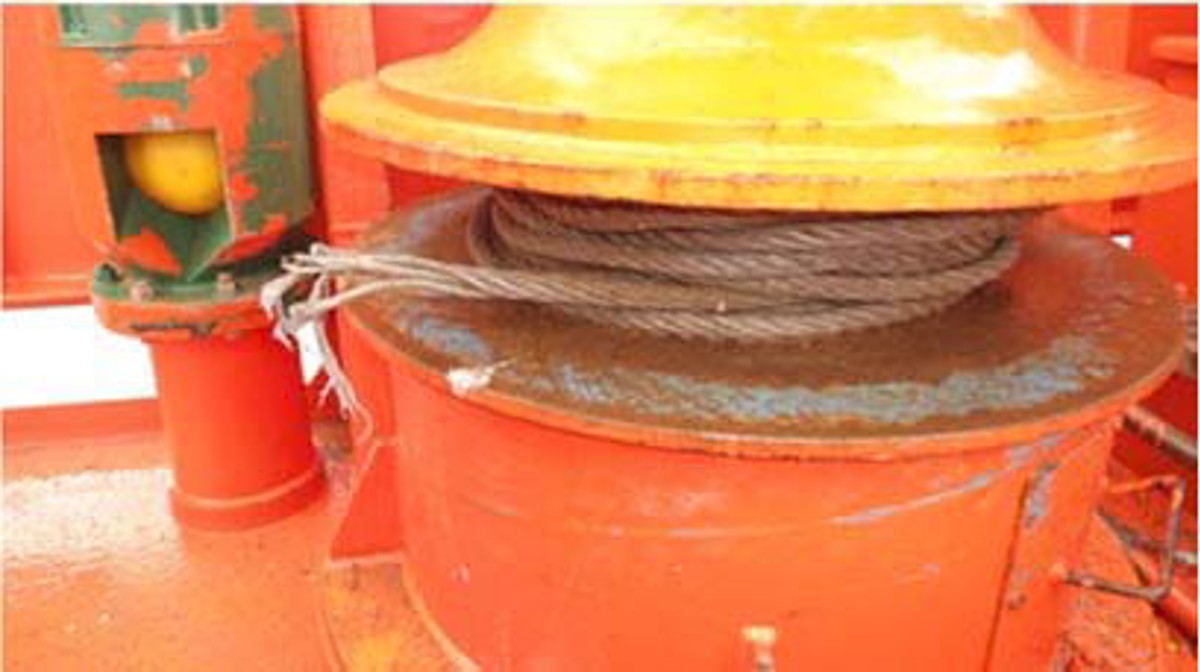
capstan showing parted wire
Findings
Our Member’s investigation noted the following:
- A clear deck policy was constantly followed.
- The certified safe working load (SWL) of the capstan wire was below the rated pull.
- Tear and wear – friction of capstan wire rope on the edging of capstan flanges.
- There had been no visual checks for tear and wear of wires made by the crew after each anchor drag test.
- Another, more preferable and safer, option of using tugger winches had not been considered for this operation.
Lesson learnt
The following lessons can be learnt:
- SWL requirements should always be considered when rigging/towing operations on deck. Ensure that the capstans rated pull is below the certified SWL of the capstan wire. The capstan should stall before the wire fails.
- Anchors should be moved on deck only with tugger wires connected either through towing pins or snatch blocks fixed on the pad eyes next to the stern roller, ensuring that all pinch points for the wires are identified and avoided.
- Capstan winches should not be used as a substitute for a deck tugger.
- When using capstans, care should be taken with wire lead in and lead out angles to avoid wire abrasion from the capstan flanges.
- Avoid excessive wraps on the capstan drum which would cause knifing damage of the wire and subsequently reduce the wire SWL.
- Visual checks: checks of the tugger/capstan wires and other rigging/towing equipment should be carried out by the crew before every test, and checks made of wire ropes SWLs on other anchor handling tug supply (AHTS) vessels for any wire underrating issues to identify/investigate and address each particular case.
- Vessel should carry at least one spare tugger and certified capstan wire to allow replacement of damaged wires immediately.
- Revised risk assessment for anchor drag test operations to include identified additional hazards and control measures.
- Ensure vessel personnel involved in rigging and lifting operations receive appropriate training.
- Design/size of the stern roller to be adequate to allow the Delta Flipper type anchor to go through it easily without getting stuck.
Members may wish to refer to the following similar incidents (key words: wire, parted, SWL):
- Fatality during anchor handling operation
- Near-miss: Dropped taut wire clump weight
IMCA Safety Flashes summarise key safety matters and incidents, allowing lessons to be more easily learnt for the benefit of the entire offshore industry.
The effectiveness of the IMCA Safety Flash system depends on the industry sharing information and so avoiding repeat incidents. Incidents are classified according to IOGP's Life Saving Rules.
All information is anonymised or sanitised, as appropriate, and warnings for graphic content included where possible.
IMCA makes every effort to ensure both the accuracy and reliability of the information shared, but is not be liable for any guidance and/or recommendation and/or statement herein contained.
The information contained in this document does not fulfil or replace any individual's or Member's legal, regulatory or other duties or obligations in respect of their operations. Individuals and Members remain solely responsible for the safe, lawful and proper conduct of their operations.
Share your safety incidents with IMCA online. Sign-up to receive Safety Flashes straight to your email.