Luff ram clevis failures
- Safety Flash
- Published on 18 January 2013
- Generated on 26 December 2024
- IMCA SF 01/13
- 2 minute read
Jump to:
A member has reported a number of incidents in which a luff ram has parted at the clevis.
What happened?
The first incident occurred during loading test of a remotely operated vehicle (ROV) system.
During recovery of the ROV whilst latched into the snubber, another luffing ram on the same launch and recovery system (LARS) parted in the same manner.
Subsequently, during an ROV launch of the same system, the replacement starboard luffing ram parted at the clevis. There were no injuries or damage to equipment.
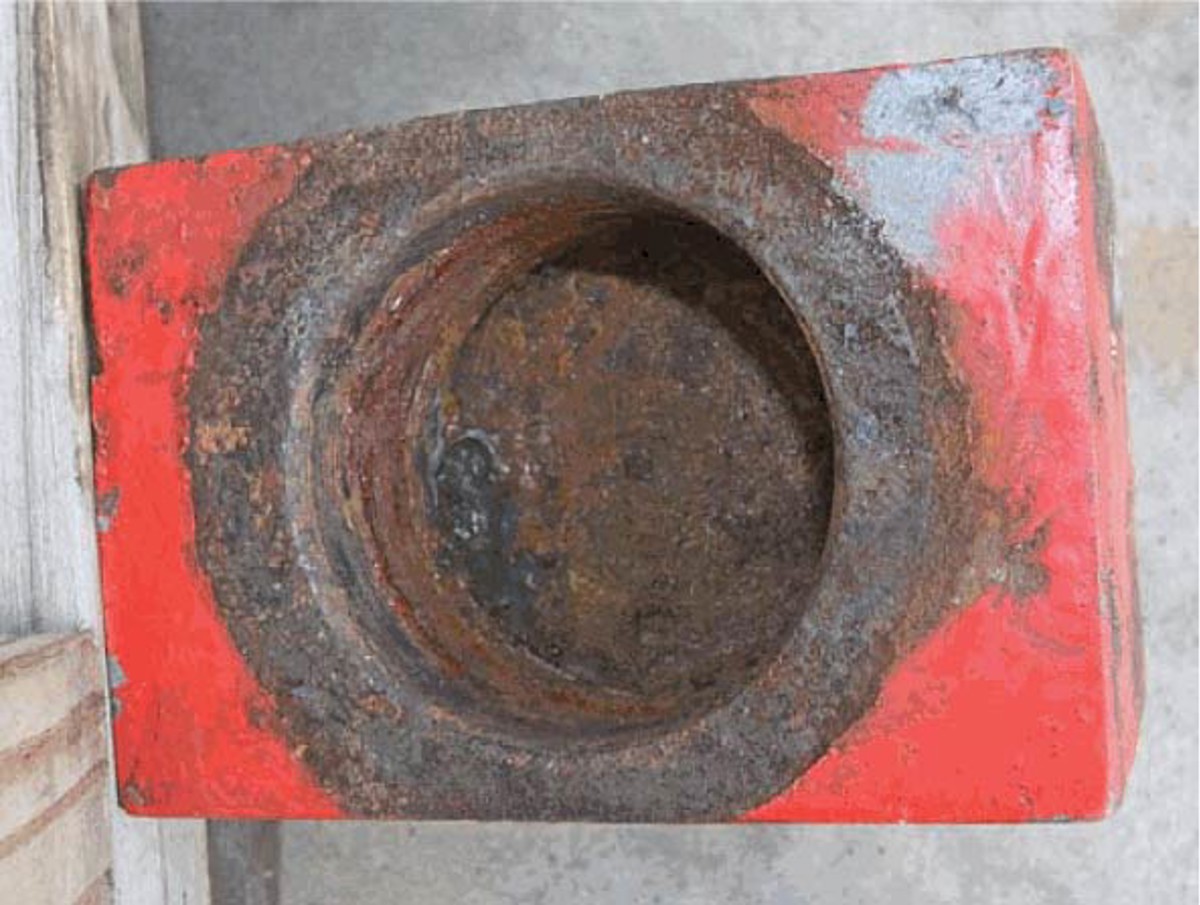
Clevis pictured after failures
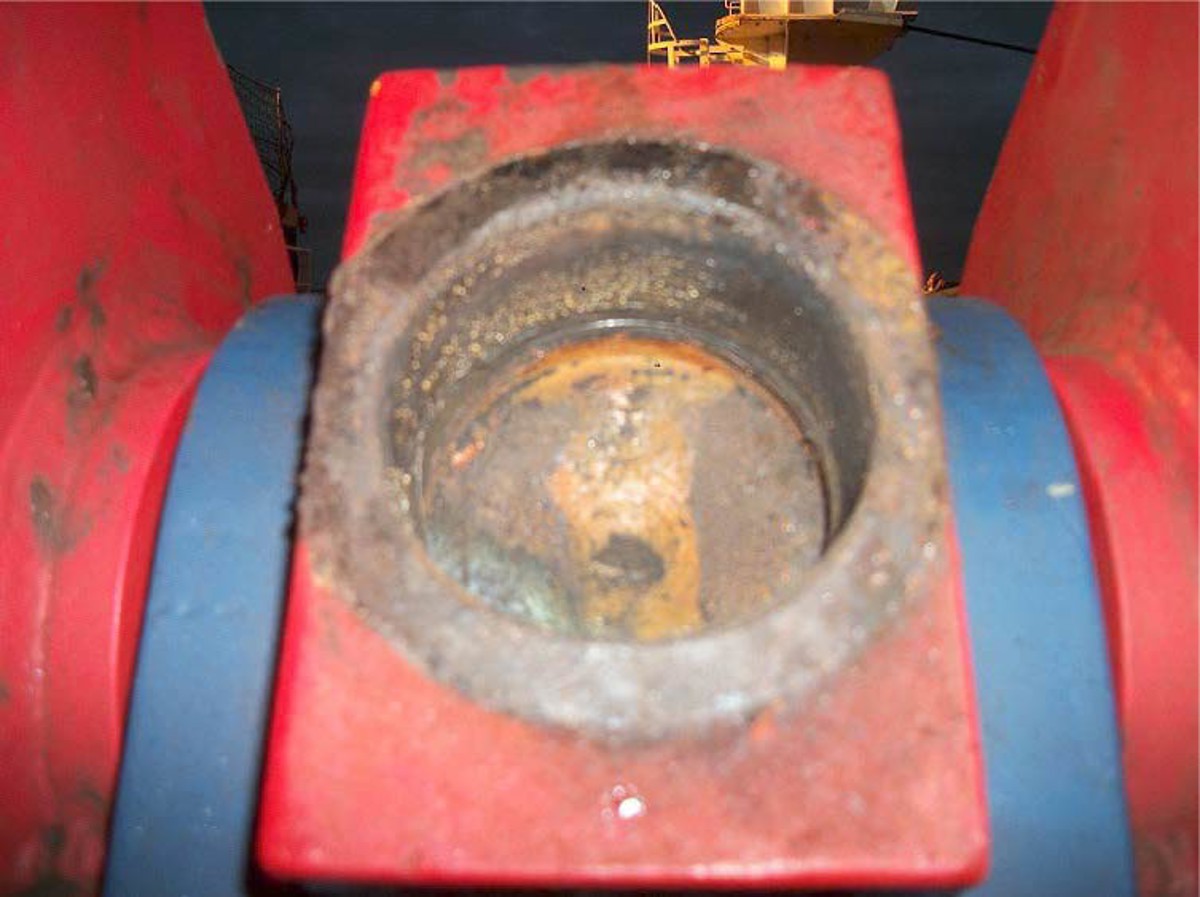
Clevis pictured after failures
What were the causes?
An investigation identified the following:
Contributory factors:
- No evidence of anti-seize compound or other corrosion inhibitor in the rod end threads or on the rod threads.
- Dead space between rod eye and cylinder rod allows generation and collection of moisture/condensation.
Immediate causes:
- Excessive corrosion of each clevis (rod eye).
- Dimensional check shows clevis to be deformed.
The company notes that root cause analysis for multiple failures is on-going; however, the causes of the corrosion are in part attributable to a missed step during service and maintenance of the cylinders.
Actions
The following actions were taken:
- the planned maintenance system was updated with the manufacturer’s recommendations for inspection of cylinder rod eyes:
- while A-frame foot is approximately 1″ from the hard stop so the luff cylinders are in tension, use a feeler gauge to determine if there is any gap between the faces of the rod eye and rod (there should be zero gap). If there is a gap, the cylinder should be removed, rod eye removed and inspected
- verify that counterbalance valves are adjusted properly
- perform a visual inspection of the A-frame operation to focus on cylinder timing or excessive lateral movement
- perform a visual inspection of the rod eye surface for excessive signs of corrosion at point of rod entry.
- while A-frame foot is approximately 1″ from the hard stop so the luff cylinders are in tension, use a feeler gauge to determine if there is any gap between the faces of the rod eye and rod (there should be zero gap). If there is a gap, the cylinder should be removed, rod eye removed and inspected
IMCA Safety Flashes summarise key safety matters and incidents, allowing lessons to be more easily learnt for the benefit of the entire offshore industry.
The effectiveness of the IMCA Safety Flash system depends on the industry sharing information and so avoiding repeat incidents. Incidents are classified according to IOGP's Life Saving Rules.
All information is anonymised or sanitised, as appropriate, and warnings for graphic content included where possible.
IMCA makes every effort to ensure both the accuracy and reliability of the information shared, but is not be liable for any guidance and/or recommendation and/or statement herein contained.
The information contained in this document does not fulfil or replace any individual's or Member's legal, regulatory or other duties or obligations in respect of their operations. Individuals and Members remain solely responsible for the safe, lawful and proper conduct of their operations.
Share your safety incidents with IMCA online. Sign-up to receive Safety Flashes straight to your email.