Lack of maintenance caused a problem involving the bus tie breaker
- DP Event
- Published on 27 February 2018
- Generated on 29 April 2025
- DPE 01/18
- 2 minute read
Undesired event
Jump to:
The maintenance requirements of some major DP components were not included in the vessel's computerised Planned Maintenance System.
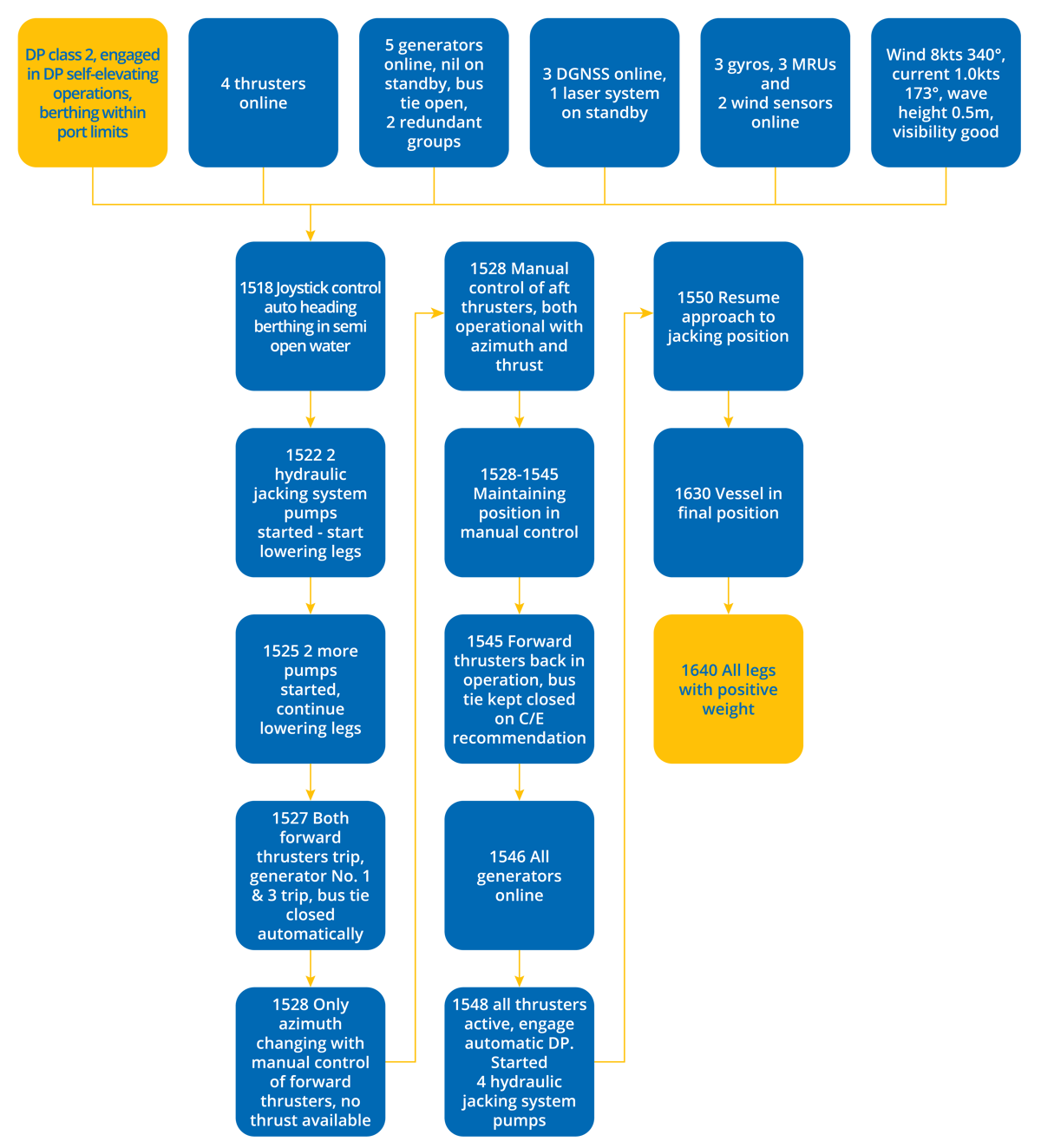
Comments
The power management system was set for semi-automatic mode as required for DP2 operations.
Uncontrolled and unsynchronised closure of the bus tie breaker resulted in simultaneous trip of DG1 and DG3 with a consequence that the forward thrusters tripped.
Based on conclusions from the technical analysis, the primary reason (root cause) of the event had been identified as lack of maintenance of the DP critical system(s) more precisely the bus tie breaker.
The ship was provided with a computerised planned maintenance system (PMS) which should cover all maintenance activity on board. The maintenance requirements of some major DP components were not included in the PMS.
Considerations
- From the information supplied, there was minimal DP stabilisation period allowed for at the start of the operation or following recovery when the vessel again engaged DP control.
- It took 18 minutes to restore both forward thrusters – could this have been achieved more quickly?
- It is assumed that a partial blackout occurred, causing loss of both forward thrusters – normally the thrusters would be arranged such that the worst case failure (WCF) would cause the loss of one forward and one aft thruster.
- It appears that the control of the thrusters was taken manually, however it should be questioned whether the automatic DP system or JSAH would have maintained the vessel in position.
- While post-failure recovery time is definitely an issue, it seems that vessel design and operating configuration could be the root causes.
- The event does highlight the importance of identifying and maintaining all items of critical operational equipment.
Latest DP incidents
-
Thorough preparation is key
With 4 of 8 diesel generators running and connected to a closed ring bus, and 7 of the 8 thrusters selected to DP, a DP equipment class 3 MODU was set up in Green mode whilst on standby.
DPE 03/24
5 November 2024
Incident
-
There – but not really there
This DP event occurred on a DP equipment class two supply vessel whilst carrying out cargo operations on the starboard side alongside the asset and working at the lee side in the drift-off position.
DPE 03/24
5 November 2024
Incident
-
Equipment Class 3, even if you operate as 'Class 2'
This case study examines a DP incident on an equipment class 3 multi-purpose vessel while operating in good conditions.
DPE 03/24
5 November 2024
Incident
-
Line of sight
This case study covers events onboard a DP equipment class 2 vessel whilst holding position in a turbine field, with three position reference systems selected into DP – DGPS, HPR and Fanbeam.
DPE 03/24
5 November 2024
Incident
-
DP Drill Scenario
DP emergency drill scenarios are included to assist DP vessel management, DPOs / Engineers, and ETOs in conducting DP drills onboard.
DPE 03/24
5 November 2024
Incident
The case studies and observations above have been compiled from information received by IMCA. All vessel, client, and operational data has been removed from the narrative to ensure anonymity. Case studies are not intended as guidance on the safe conduct of operations, but rather to assist vessel managers, DP operators, and technical crew.
IMCA makes every effort to ensure both the accuracy and reliability of the information, but it is not liable for any guidance and/or recommendation and/or statement herein contained.
Any queries should be directed to DP team at IMCA. Share your DP incidents with IMCA online. Sign-up to receive DP event bulletins straight to your email.