Equipment Class 3, even if you operate as 'Class 2'
- DP Event
- Published on 5 November 2024
- Generated on 2 July 2025
- DPE 03/24
- 4 minute read
Incident
Jump to:
This case study examines a DP incident on an equipment Class 3 multi-purpose vessel while operating in good conditions.
1. Overview
The vessel was set up according to their class-approved FMEA in a ‘DP 2 configuration’ with open bus ties, four of the six generators running online, and equally split across two bus sections.
The FPSO they were due to attend had a holdback Tug connected to allow more control during operations.
2. What happened?
The vessel was 100 m from the FPSO and approaching when a failure alarm was initiated for Main Engine 1. This rapidly escalated to losing the port switchboard followed by the starboard switchboard almost simultaneously.
In its blacked-out condition, the vessel proceeded to drift away from the asset due to the correct procedures being followed and being set up in a drift-off position.
The vessels Bridge department immediately contacted the FPSO to warn of the emergency, and the FPSO lowered the starboard side Yokohama’s in case of impact between the vessels.
The anchors and towing lines were prepared as the engine department proceeded to fault find and regain power to the vessel. The Tug was called to disconnect from the FPSO and standby for towing, if necessary.
The engineers discovered water in the fuel system, within the settling and service tanks on both port and starboard sides. and were required to drain the water from both systems. After two hours, the engines were finally restarted, and the vessel returned under control, having lost 2nm position.
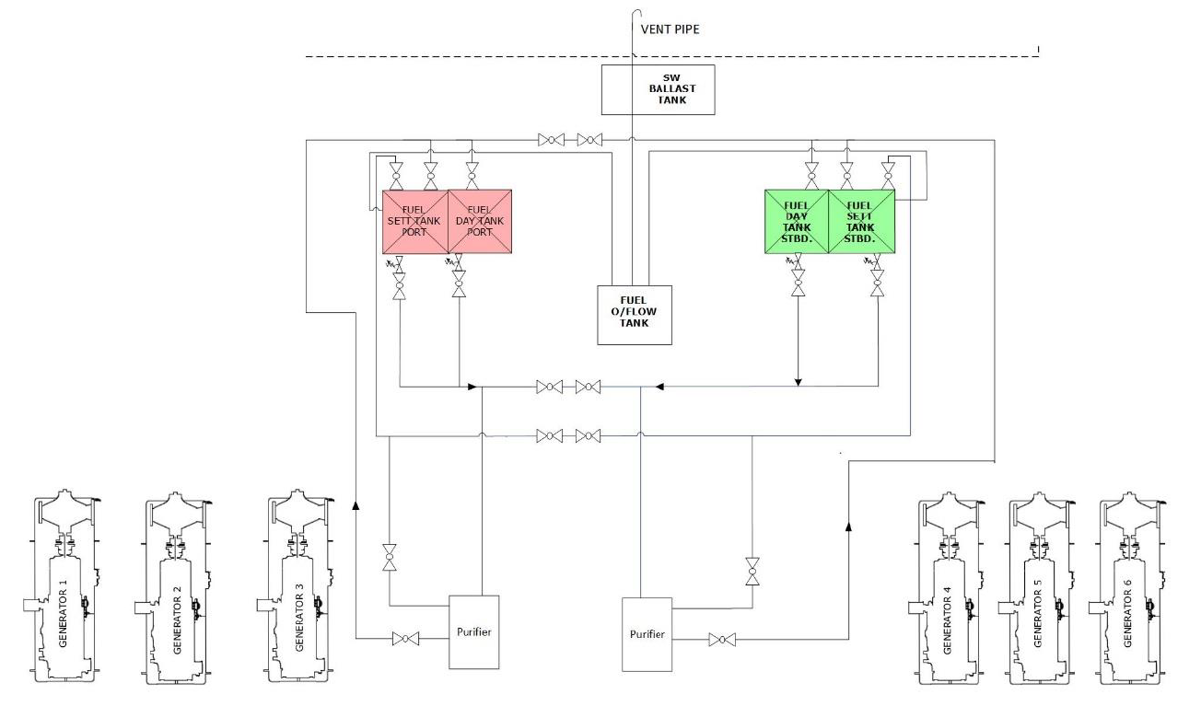
Figure 4 – Simplified example fuel system
3. Findings
Investigation of the event uncovered a few areas to consider:
- The water ingress to the FO overflow Tank was traced back to the FO overflow tank vent pipework.
- The FO overflow tank vent pipe was traced and found to pass through a water ballast tank, which at the time was full.
- Upon emptying the water ballast tank, the leaking stopped, and when the vent pipe was safely inspected, it was found with several holes from years of corrosion.
- The FO overflow tank was set up to the port and starboard settling tanks simultaneously.
- FO operation procedures were reviewed, and concluded that there was room for improvement in regard to the storage, transfer and treatment onboard.
- During the incident, both port and starboard FO purifiers were operating; however, no alarms were activated.
- An investigation of purifier settings revealed that the water monitoring function was inactive in a factory setting. The Purifier controller was still in default factory settings, which did not match the vessel's separator type onboard. The controller settings were updated per the manufacturer's instructions to match the actual purifiers onboard. All functions and alarms, including water content alarm, were verified.
4. Considerations
Though the vessel was operating in a configuration they referred to as ‘DP 2 mode’ the vessel is constructed following the classification for DP equipment class 3. Therefore, a loss of a static component, i.e. a pipe, should not result in a loss that could exceed the worst-case failure design intent.
The main cause for this incident was clear: power failure led to the loss of thrusters and subsequent position, but what about secondary failure, the failure mode that started it all?
- Would you have called it a mechanical or human factor?
- Was it the hole in the vent pipe? But if the vent pipe hadn’t run through a water ballast tank, the hole wouldn’t have caused such an issue.
- Was it that the pipe should have been picked up at the design/construction stage, and could the FMEA have picked this potential failure out?
- Was it the incorrect set-up of the FO overflow tank valves, for if they’d been set up differently, only one redundancy group would have been affected, no matter that the water was there?
- Was it the FO procedures being followed onboard?
- Was it that the purifiers were in the default factory setting? Had the settings been different, would the water content have been identified before the water affected the engine's combustion cycle?
So, was this mechanical, or was it a human factor?
Latest DP incidents
-
Complete the job
Whilst connected to a turbine, an alarm was generated on the DP operator station, ‘Unbalanced load on SWBD 1’.
DPE 01/25
16 January 2025
Undesired event
-
How is your alignment?
Loss of the CyScan position reference system generated a reference system failure alarm and moments later the vessel began to lose position with the accompanying alarms.
DPE 01/25
16 January 2025
Incident
-
Beware your centre of rotation
The stern thrusters started to oscillate which transferred to an oscillating motion of the vessel and high forces were being used to try to maintain position.
DPE 01/25
16 January 2025
Incident
-
A-Tension
Whilst pipelaying in shallow water, the vessel experienced a tension sensor failure on one tensioner.
DPE 01/25
16 January 2025
-
DP Drill Scenario
DP emergency drill scenarios are included to assist DP vessel management, DPOs / Engineers, and ETOs in conducting DP drills onboard.
DPE 01/25
16 January 2025
Drill Scenario
The case studies and observations above have been compiled from information received by IMCA. All vessel, client, and operational data has been removed from the narrative to ensure anonymity. Case studies are not intended as guidance on the safe conduct of operations, but rather to assist vessel managers, DP operators, and technical crew.
IMCA makes every effort to ensure both the accuracy and reliability of the information, but it is not liable for any guidance and/or recommendation and/or statement herein contained.
Any queries should be directed to DP team at IMCA. Share your DP incidents with IMCA online. Sign-up to receive DP event bulletins straight to your email.