DP3 drillship switchboard blacked out
- DP Event
- Published on 3 September 2019
- Generated on 8 July 2025
- DPE 03/19
- 4 minute read
Undesired event
Jump to:
A DP3 6th generation drillship was set up on automatic DP engaged in plug and abandonment operations in field.
Overview
A DP3 6th generation drillship was set up on automatic DP engaged in plug and abandonment operations in field.
The DP design concept of the vessel was such that there were two redundant groups and the vessel was set up with power generation and thruster supplies equally split across each redundant group with main bus ties open.
Weather conditions at the time of the event were acceptable based on the capability of the vessel and there was at least one generator on standby on both Port and Starboard 11kV switchboards.
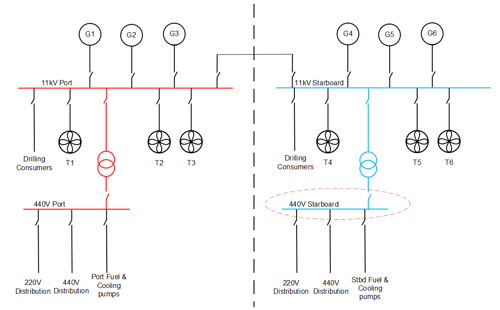
Without warning, the Starboard 440V switchboard blacked out leading shortly after to the 11kV switchboard blacking out resulting in loss of power to all the respective main thruster drilling and auxiliary consumers. The Port switchboard remained online, and the vessel remained in position. Drilling operations were immediately suspended, and safety measures were actioned while the blackout was investigated, and power fully restored.
Investigation revealed that the loss of power generation on the 11kV switchboard leading to its blackout was caused by fuel pump failure and subsequent fuel starvation on the online Starboard engines. Fuel pump failure (and cooling water auxiliaries) was caused by the initial 440V starboard switchboard failure. The fuel starvation also meant that automatic blackout recovery measures (standby starting of offline generators) were unsuccessful.
The root cause of the loss of power to the Starboard 440V switchboard was found to be a faulty under voltage coil in the main supply circuit breaker. The fault causing the circuit breaker to open.
Lessons learned
The investigation noted that the main circuit breakers on the 440V switchboards were obsolete and no longer supported by the original equipment manufacturer. Although a spare was sourced onboard the vessel, the event triggered a full review of onboard critical spares and the implementation of a regular third-party inspection and testing regime over and above normal crew maintenance routines. The investigation also noted that budgets were being worked on for full replacement of all 440V main circuit breaker at the next SPS docking.
Although fitted, the air powered emergency fuel pump provided no benefit during the main power supply failure. The investigation revealed that the pumps operation was not as analysed within the vessel’s DP FMEA and a programme of testing was planned at the soonest opportunity to ensure correct functionality/operation. The findings of such testing would feed back into the vessel’s DP FMEA and any other relevant operations manuals and checklists.
The investigation considered drilling consumer supplies and noted that drilling variable speed drives were not segregated in line with the vessel’s redundancy concept meaning that 50% of the drive cooling system were cross connected. The effect of this during the event was only unnecessary loss of consumers to the drilling system. In different circumstances, this cross connection may have impeded safety precautions being implemented or brought unnecessary risk to the DP system redundancy concept. The investigation report recommended that the drilling system distribution be reviewed with cross connections in mind and any enhancements actioned thereafter.
Conclusion
This case study demonstrates the importance of good understanding of the DP system and its redundancy concept such that in the event of a failure, sufficient confidence in the system exists to permit a safe outcome with no loss of position.
The case study also demonstrates the importance of a high quality FMEA and associated testing regime to not only ensure the redundancy concept is intact but also that backup and recovery systems operate appropriately.
Finally, the importance of considering mission equipment integration in conjunction with the DP system redundancy concept should not be underestimated as the consequence of poor integration could be significant or greater than a loss of position.
Latest DP incidents
-
Complete the job
Whilst connected to a turbine, an alarm was generated on the DP operator station, ‘Unbalanced load on SWBD 1’.
DPE 01/25
16 January 2025
Undesired event
-
How is your alignment?
Loss of the CyScan position reference system generated a reference system failure alarm and moments later the vessel began to lose position with the accompanying alarms.
DPE 01/25
16 January 2025
Incident
-
Beware your centre of rotation
The stern thrusters started to oscillate which transferred to an oscillating motion of the vessel and high forces were being used to try to maintain position.
DPE 01/25
16 January 2025
Incident
-
A-Tension
Whilst pipelaying in shallow water, the vessel experienced a tension sensor failure on one tensioner.
DPE 01/25
16 January 2025
-
DP Drill Scenario
DP emergency drill scenarios are included to assist DP vessel management, DPOs / Engineers, and ETOs in conducting DP drills onboard.
DPE 01/25
16 January 2025
Drill Scenario
The case studies and observations above have been compiled from information received by IMCA. All vessel, client, and operational data has been removed from the narrative to ensure anonymity. Case studies are not intended as guidance on the safe conduct of operations, but rather to assist vessel managers, DP operators, and technical crew.
IMCA makes every effort to ensure both the accuracy and reliability of the information, but it is not liable for any guidance and/or recommendation and/or statement herein contained.
Any queries should be directed to DP team at IMCA. Share your DP incidents with IMCA online. Sign-up to receive DP event bulletins straight to your email.