Main crane hoist wire damage
What happened?
A 70-centimetre length of main crane hoist wire was found to be damaged during an inspection. During pile installation operations, small plastic items were observed to be attached to the 400te crane main wire. The plastic was identified as ducting, a protection barrier from water/grease spray when recovering or paying out the crane wire within the crane pedestal.
After internal consultation with both company technical specialists and the offshore management team, it was decided to cut 1,410 meters of wire rope from the hook subsea using an ROV. The crane wire re-socketing was then performed onboard the vessel main deck. This work cost 71 hours of downtime.
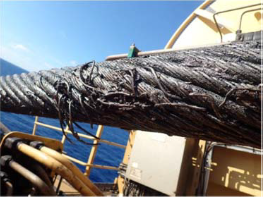
Findings
- A contact/rubbing point was identified on the knuckle aperture where the crane wire passed through the knuckle boom;
- The crane operator struggled to engage the Active Heave Compensation (AHC) and proceeded to disengage the auto knuckle function to activate AHC;
- The crane operator ignored the angle deviation alarm and did not notify the lay technician of any issues;
- The resultant knuckle position extended beyond the working parameters of the special lift mode which caused the crane wire to contact the knuckle aperture. When AHC was activated, it created a sawing motion against the inner side of the aperture which over a period of lifting operations damaged the wire rope and cut a groove into the aperture structure;
- The event occurred 3 days before the plastic was observed on the wire;
- The crane manufacturer was not able to provide crane familiarisation to the crane operator onboard the vessel due to COVID-19 travel restrictions. The company crane operator familiarisation checklist was completed onboard;
- The crane operator had knuckle boom experience and possessed a crane trainer/assessor qualification;
At the time of the incident, the crane operating system displayed a KN-Boom Auto virtual button with no other information when selected. The crane manufacturer subsequently recommended to upgrade the system to enable a pop-up screen showing the limits in special lift mode when the KN-Boom Auto virtual button is selected.
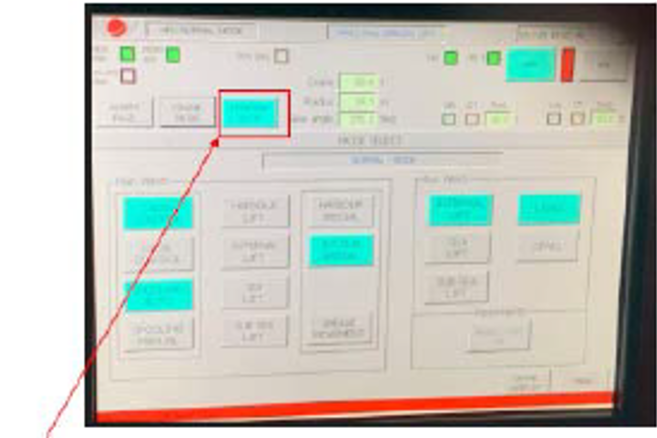
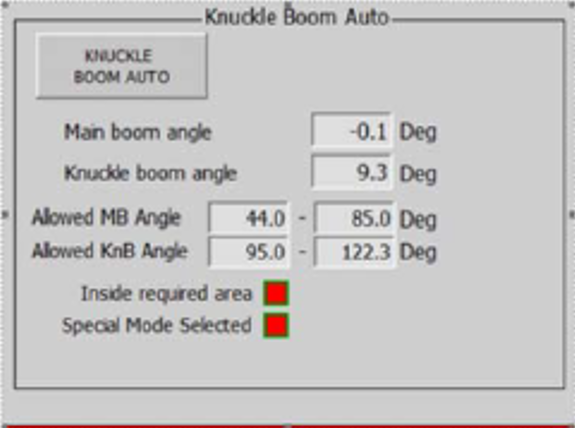
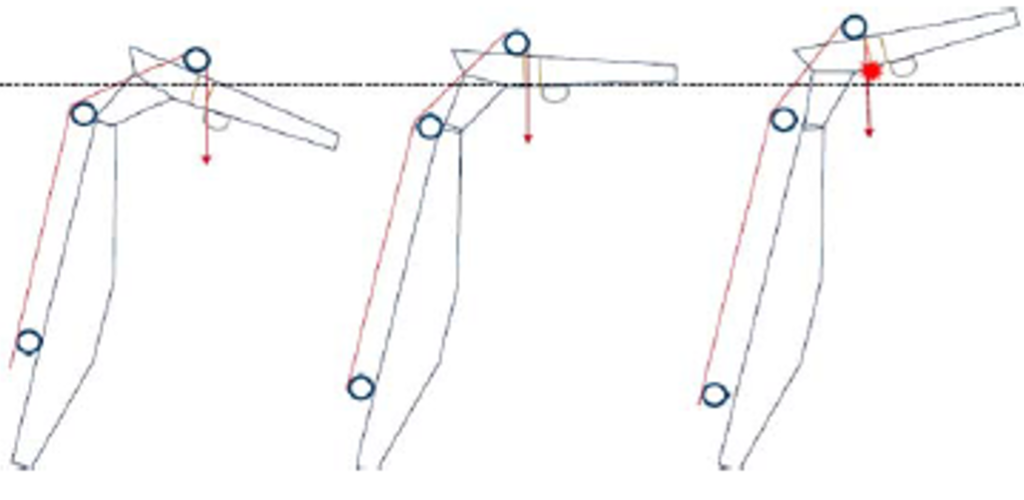
Illustration 2 shows the correct position of the knuckle boom, i.e. in a horizontal position with the main wire inside the aperture
Illustration 3 shows the knuckle boom in an angle exceeding 114.56 degrees, at which point the wire touches against the aperture
Actions taken? Lessons learned?
- Reinforce to equipment operators the importance of always adhering to equipment manufacturer’s instructions and raising any issues that are experienced;
- Review similar equipment to verify whether operating systems can be improved to optimize the human/machine interface.
Members may wish to refer to
- Crane Wire Failure [“investigation has shown that the crane wire was weakened by the hook being drawn fully up into the sheave at the end of the crane, then the crane articulated sections operated in a manner that over stressed the wire.”]
- Crane Wire Failure
- Catastrophic Failure of vessel main crane wire
Safety Event
Published: 10 November 2020
Download: IMCA SF 31/20
IMCA Safety Flashes
Submit a Report
IMCA Safety Flashes summarise key safety matters and incidents, allowing lessons to be more easily learnt for the benefit of all. The effectiveness of the IMCA Safety Flash system depends on Members sharing information and so avoiding repeat incidents. Please consider adding [email protected] to your internal distribution list for safety alerts or manually submitting information on incidents you consider may be relevant. All information is anonymised or sanitised, as appropriate.
IMCA’s store terms and conditions (https://www.imca-int.com/legal-notices/terms/) apply to all downloads from IMCA’s website, including this document.
IMCA makes every effort to ensure the accuracy and reliability of the data contained in the documents it publishes, but IMCA shall not be liable for any guidance and/or recommendation and/or statement herein contained. The information contained in this document does not fulfil or replace any individual’s or Member's legal, regulatory or other duties or obligations in respect of their operations. Individuals and Members remain solely responsible for the safe, lawful and proper conduct of their operations.